Polymeric membrane materials for CO2-selective
separation (I)
Hao Jihua
(Department of Chemical Engineering, Tsinghua University, Beijing 100084, China )
Received Apr. 13, 2000.
Abstract Polymeric membrane materials for
CO2-selective separation have been reviewed. On the basis of the introduction
to solution-diffusion transport mechanism of gases in solid polymeric membranes, transport
characteristics of CO2 were summarized. CO2-selective polymeric
membrane can be divided into four types, including the chemical and physical modification
of the traditional membrane materials, polymer blending, the design and synthesis of new
membrane materials and organic-inorganic hybrid membrane. Finally, the research topics in
future were also suggested.
Keywords membrane; carbon dioxide;
CO2-selective separation is a very
important problem in many fields, such as environment, petrochemical engineering,
agriculture and other relative industry.[1-16] One of the promising techniques
is membrane processes. Because of the potential economy of the membrane technology, many
governments have initiated and extensively focused in the projects on the CO2-selective
polymeric membranes and membrane processes. Membranes and membrane processes for the
separation of CO2 and H2S from natural gases have been a project
under the "BRITE"(Basic Research in Industrial Technology for Europe) formed as
a European Community R&D program in the middle of 1980s.[5] In Japan,
membrane processes for CO2-selective separation has been an important project
under C1 Chemistry "Sunshine" plan.[6] In China, membrane processes
for CO2/CH4 separation have been studied because of the existence of
several large sour natural gas fields and application in tertiary oil recovery.[7]
A number of large American companies first applied the membrane technology for separation
of CO2/CH4 and continued efforts on new membrane materials and
membrane process design for CO2 separation.[8] The membranes for CO2-selective
separation have made much progress during this period.
Because earlier cellulose acetate membrane for reverse osmosis could be
easily adapted to form dry asymmetric structures using solvent-exchange dehydration for
gas separation, especially Monsanto invented "caulked membrane" successfully for
recovery of hydrogen from ammonia purge gas, solid polymer-based membranes for gas
separation have been paid attention to in the membrane field over the past twenty years.
New polymeric membrane formation with integrally-skinned dense thin asymmetric structure
have been the main research topics.
There have been two kinds of polymeric membrane for CO2-selective
separation processes. One is the solid polymeric membrane based on the solution-diffusion
mechanism, another is the facilitated transport membrane based on the
solution-reaction-diffusion mechanism.[17]
In this review we limited only to membrane materials
based on the solution-diffusion mechanism.
1 TRANSPORT MECHANISM OF GASES IN SOLID
POLYMERIC MEMBRANES AND CHARACTERISTICS OF CO2
The permeation of a gas molecule through a dense polymer membrane proceeds by a
solution-diffusion mechanism. In this model, gas molecules first dissolve into the high
pressure face of the membrane, diffuse across the membrane to the low pressure side, and
desorb from the face.[18, 19]
The permeability coefficient P of a membrane in solution-diffusion
processes can be represented as the product of a diffusivity [D] and solubility [S]
coefficient as shown in the following equation.
P=[D][S]
The ideal selectivity can be expressed as
αAB=PA/PB=[DA/DB][SA/SB]
Where, [DA/DB]---------the diffusivity selectivity
[SA/SB]----------the
solubility selectivity
In addition to operating conditions (i.e. temperature, pressure and
composition), gas solubility also depends on factors such as penetrant interactions, and
polymer morphology(i.e. crystallinity, orientation, etc.).[20] Gas diffusivity
depends on the ability of small gas molecules to undergo diffusive jumps which occur when
thermally driven, random, cooperative polymer segmental dynamics from transient gaps,
large enough to accommodate penetrants, in the immediate vicinity of the gas molecules.[21]
Like solubility, diffusivity depends on membrane operating conditions; moreover, gas
diffusivity is also sensitive to properties such as penetrant size, polymer morphology and
polymer segmental dynamics.
2 CHARACTERISTICS OF CO2 AND CH4
2.1 Gas condensibility
In most polymers, CO2(Tc=31°C) is more soluble than CH4
(Tc=-82.1°C). Gas critical temperature, Tc, normal boiling point, Tb,
and Lennard-Jones force constant are all measures of condensibility which correlate well
with the solubility coefficients of a range of penetrants in polymers. Gas solubility in
polymers generally increases with increasing gas condensibility.[22, 23]
2.2 Penetrant size and shape
Diffusion coefficients in polymers are sensitive to penetrant size and shape. The
diffusivity of linear or oblong penetrant molecules such as CO2 is higher than
the diffusivities of spherical molecules of equivalent molecular volume. The van der Waals
volumes of CO2 and CH4 are estimated to be 17.5 and 17.2 cm3/mole.[22,
24] These molecular volumes yield equivalent spherical diameters of 3.33 and 3.31Å
for CO2 and CH4, respectively. But the diffusion coefficient of CO2
is typically greater than that of CH4, despite the larger van der Waals volume
of CO2. The kinetic diameter of the asymmetric molecule CO2 (3.30Å)
is smaller than that of methane, a symmetric molecule (3.80Å). Based on such results, the
transport of small, asymmetric molecules is understood to proceed with diffusion jumps of
the penetrant through a polymer occurring principally parallel to the long axis of the
penetrant.
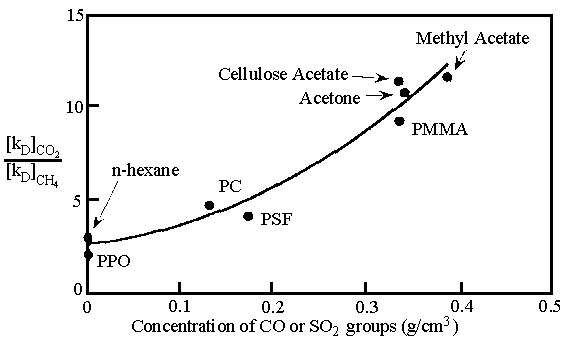
Fig. 1. The effect of polar carbonyl and
sulfone group concentration on CO2/CH4 solubility[25]
Most glassy gas separation
membrane materials achieve high permselectivity as a result of high diffusivity
selectivity (i.e. by sieving penetrant molecules based on differences in molecular size).
2.3 Polarity
Gas solubility is sensitive to specific interactions between gas and polymer molecules.
Gases such as CO2, which has a quadrupole moment, are in general, more soluble
in polar polymers. Many polymeric materials for CO2-selective membrane have
been designed by use of this property. Van Amerongen determined that the solubility of
quadrupolar CO2 increased substantially as acrylonitrile content increased.[25]
Pilate suggested that CO2 interact favorably with the sulfone group in
polysulfone via induced dipole-dipole interaction.[26] In this regard, Koros
found a correlation between CO2/CH4 solubility selectivity and the
concentration of polar carbonyl and sulfone groups in the medium in which the gases were
dissolved.[27] These data are reproduced in Fig. 1.[25] In a related
work, Chern and coworkers found that aryl nitration of polysulfone, which adds polar nitro
groups to the polymer backbone, increases CO2/CH4.[28]
2.4 Pressure
Permeability of CO2 in polymeric membrane is more sensitive to pressure. The
selectivity of CO2/CH4 mixture in the most of the current polymeric
membranes decreased at high pressure because of the membrane plasticization. This is one
of the key problems to be solved for CO2-selective polymeric membrane.
At very high gas pressure, permeability may increase with increasing
pressure. This increase is related to penetrant plasticization of the polymer matrix and
is primarily due to an increase in the penetrant diffusion coefficient. The data in Fig. 2
present plasticization in the presence of CO2.[22, 29] Other
condensable gases and hydrocarbon vapors can also plasticize polymers. At sufficiently
high pressure the penetrant acts as an efficient plasticizer in hydrophilic polymers such
as polyvinyl alcohol. The permeability decreases with pressure initially, consistent with
the prediction of dual mode model, and then increases when the gas begins to plasticize
the polymer. Plasticization occurs when penetrant molecules dissolve in the polymer chain
segmental motion. The increased segmental mobility may be observed by a depression of the
glass transition temperature of the polymer-penetrant mixture. The increased segmental
mobility provides more opportunities for penetrant molecules to execute diffusive jumps,
and, in turn, the penetrant diffusion coefficient increases. Plasticization is undesirable
for most gas separation membranes since the polymers used in these applications depend
largely on diffusivity selectivity to achieve high overall permselectivity. The relatively
large, uncontrolled polymer segmental motions associated with the plasticized or rubbery
polymers decrease the diffusivity selectivity and, therefore, overall permselectivity of
polymer.
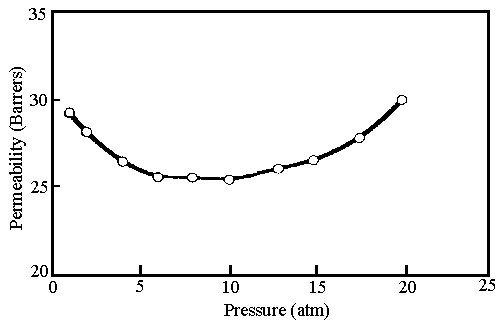
Fig. 2 CO2 induced plasticization
of poly(tetrabromophenolphthalein) at 35°C[27]
3 POLYMERIC MEMBRANE MATERIALS FOR SEPARATION
OF CO2/CH4
Much effort has been spent to optimize CO2-selective polymeric membranes:
including the chemical and physical modification of current membranes,[30, 31, 32]
blending,[33, 34] the design and synthesis of new membrane material[35,
36] and organic-inorganic membrane.[37]
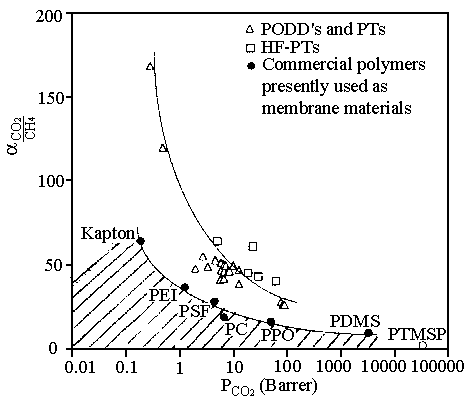
Fig. 3 "Trade-off" curves for the CO2/CH4
separation system
A typical
"trade-off curve" between CO2/CH4 permselectivity and CO2
permeability is pressured in Fig. 3.[38] A crosshatched, undesirable area,
below the solid line is associated with "low free volume glasses" and
"rubbery polymers". The poor mobility selectivities and high diffusivities in
rubbery media noted earlier produce high permeabilities and low overall permselectivities.
On the other hand, the well-packed, low free volume glasses, give equally unattractively
low permeabilities and high selectivities. The solids line (-.-)
represents "optimistic" tradeoff behavior typical of commercially available
engineering resins.
During the past decade many investigators attempted to synthesize
entirely new polymers that exhibit both a higher permeability and a higher selectivity
than presently available polymers. Or they attempted to enhance the selectivity and/or
permeability of available polymers by chemical or physical modification.
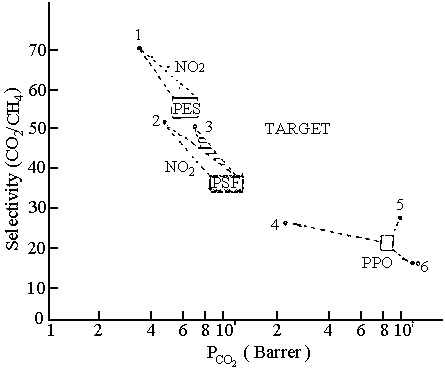
Fig. 4 Influence of chemical modification
Quite a lot of modification have
been carried out to those polymers that are proven gas separation materials. [30, 31,
32] Stam et al. modified on-chain of polymers, like polysulfone (PSF),
polyethersulfone (PES) and poly(phenylene oxide) (PPO) by substitution of aromatic
protons, i.e. by means of nitration, silylation, bromination of alkyl groups and
acrylation.[30] Some results are shown in Fig. 4. Even modifications with more
complex chemicals have not shown the desired result.
Kesting et al. improved the flux of polysulfone gas separation
membranes by using Lewis acid-base pairs in the aqueous phase inversion bath. The
resulting membranes possessed greater free volume and hence, higher flux, than those made
conventionally.31 In addition, Stam put additives to the polymer membrane by
physical modification. The most successful was the addition of molecular sieves(Na-Y).
Addition of 1% by weight of molecular sieve to the polymer membrane has shown a relative
improvement of 2% on the permeability without effecting the selectivity. At contents of
15% molecular sieve maximum permeability has been reached. At higher contents selectivity
was reducing again, where as permeability was not improving any further.30
Barbari treated polysulfone membrane with molecular bromine. After bromine treatment, the
selectivity of a polysulfone membrane for CO2 over CH4 was increased
over 100% at 10 atm upstream pressure with only a 36% reduction in CO2
permeability.
Although all types of chemical and physical modification showed that
selectivity or permeability could be improved, even at the expense of permeability or
selectivity, the selectivities or permeabilities themselves have not exhibited remarkably
attractive.
However, the tailor-made polymers have shown that it is possible to
move away from the traditional trade-off curve connecting the conventional membrane
materials (-D-
in Fig. 3).[38] Although considerable data and general correlations relating
structure and permeability exist, there are no truly quantitative relationships to guide
detailed structure-permeability optimization. Fortunately, qualitative rules have emerged
that date back to the pioneering work by Hoeln and his colleagues at DuPont in the 1970's.[39,
40] Simply put, when changing the structure within a family of polymers, inhibiting
intersegmental packing, while simultaneously hindering the backbone mobility tends to
produce a desirable tradeoff between productivity and permselectivity changes. Currently
this is the most reliable guide for understanding structure-mobility studies of a given
family of polymers.
Table 1 lists permeability coefficients
for CO2 and CH4 in a variety of rubbery and glassy polymers, as well
as the selectivities (ideal separation factors) of these polymers for CO2/CH4.
The high selectivities of these tailor-made polymers, such as 6FDA-polyimides,
polytriazoles, and polyoxadiazoles are assumed to originate from their rigid structure.
Their high permeability is mostly explained in terms of their high free volume, which is
due to their bulky groups preventing efficient packing. The solubility is mostly relative
to the chemical composition of the polymers.[38]
In the following section the excellent polymer materials with extra
high selectivity and/or permeability will be introduced in detail.
Table 1. Permeabilities
and selectivities of CO2/CH4 in rubbery and glassy polymers
|
Permeability
coefficient, P×1010
[cm3(STP). cm/s. cm2.
cmHg]
CO2
CH4 |
Overall
selectivity
CO2/CH4 |
Poly[1-(trimethylsilyl)-1-propyne
Poly(dimethylsiloxane)
Poly(dimethyl silmethylene)
Poly(vinyltrimethylsilane)
Poly(cis-isoprene)
Poly(butadiene-styrene)
Ethyl cellulose
Poly(phenylene oxide)
Polystyrene
Poly(ethyl methacrylate)
Bisphenol-A polycarbonate
Cellulose acetate
Bisphenol-A polysulfone
Polyetherimide(Ultem)(PEI)
PMDA-4,4'-ODA polyimide
Kapton polyimide
Poly(methyl methacrylate)
6FDA-m-DDA polyimide
poly(1,3,4-oxadiazole)(POD)
Polyaniline |
28000
4550
520
200
191
171
75.0
61.0
12.4
7.01
6.8
4.75
4.6
1.33
2.7
0.22
0.62
1.8
0.3
0.32 |
13000
1430
150
14
47.4
34.2
6.8
4.3
0.78
0.35
0.36
0.15
0.18
0.036
0.059
0.0032
0.0052
0.013
0.0018
<0.002 |
2.2
3.2
3.5
14
4.0
5.0
11
14.2
16
20
19
32
26
36.9
46
68.8
119
136
168
336 |
3.1 Improvement of the selectivity of
polymers with high permeability
3.1.1 Poly(organosiloxane)
Generally, rubbery polymers exhibit high permeabilities and low selectivity, in which
silicone polymers, and in particular poly(dimethylsiloxane) (PDMS), has received
considerable attention. The high permeability of PDMS, [-(CH3)2SiO-]n,
has been attributed to its large free volume, which may be due to the flexibility of the
siloxane (-SiO-) linkages of this polymer. Although the gas selectivity of PDMS is very
low, the structure/permeability relationships of other silicone polymers have been
systematically investigated in the last few years. These studies had the objective of
finding membrane materials that exhibit higher gas selectivity than PDMS as well as high
gas permeability.
The substitution of increasingly bulkier functional groups in the
backbone or side chains of PDMS, or the replacement of its flexible -SiO- linkages with
stiffer -SiCH2- linkages, raises the glass-transition temperature, Tg,
of the polymers.[21] This means the increase of chain-packing density. The
effects of such substitution on the relationships between the gas permeability and
selectivity of silicone polymers were listed in Table 2.
Table 2. Permeabilities
and selectivities of CO2/CH4 in rubbery and glassy polymers
|
Permeability
coefficient, P×1010
[cm3(STP). cm/s. cm2.
cmHg]
CO2
CH4 |
Overall
selectivity
CO2/CH4 |
Side-chain
modification
[(CH3)2SiO]n
(CH3C3H7SiO)n
(CH3C8H17SiO)n
[(CF3C2H4)CH3SiO]n
(C6H5CH3SiO)n
Backbone modifications
[(CH3)2Si(CH2)6Si(CH3)2O]n
[(CH3)2SiCH2]n
[(CH3)2Si-p-C6H4Si(CH3)2O]n |
4570
1520
917
1210
226
1310
542
52.3 |
1450
531
314
201
36.3
395
130
10.4 |
3.2
3.0
3.0
6.9
6.5
3.3
4.2
5.2 |
As shown in Table 2, the high CO2/CH4
selectivity of poly(trifluoropropyl methyl siloxane) [(CF3C2H4)CH3SiO]n
is due to an anomalously high CO2 solubility, which results from specific
interactions between this gas, whose molecules have a strong quadrupole moment, and the
polar fluorine-containing groups in the polymer.[41, 42]
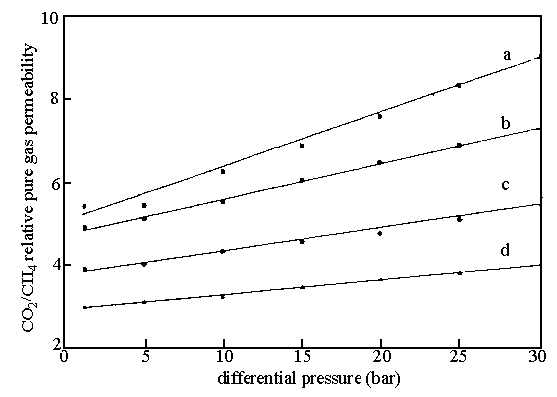
Fig.5 Effect of differential
pressure on the CO2/CH4 relative pure gas permeabilities in the
diester functionalised membranes: diester functionality (a) 30 mol%; (b) 20mol%; (c)
10mol%; (d) 0 mol%.
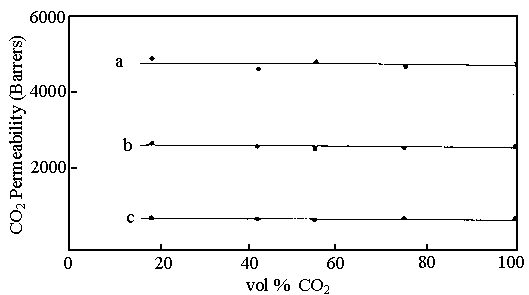
Fig.6 CO2 permeabilities coefficient at 35C and atmospheric pressure
versus composition of the CO2:CH4 permeant gas mixture in diester
functionalised membranes: diester functionality (a) 0 mol%; (b) 10mol%; (c) 30mol%.
In order to improve the
permselectivity of rubbery polymers without unacceptable loss in overall permeability via
improved solubility selectivity Ashworth et al. introduce a side-chain organofuntional
groups, such as mono- or di-ester, into a PDMS matrix.[43, 44] The increase of
selectivity results from the interaction of CO2 with the ester groups in the
ester side-chains. The results have shown in Fig. 5, 6.
In addition, the surface of poly(dimethylsiloxane) membrane was
modified by plasma treatments using Ar, N2, O2 and NH3.[45]
As a result, the selectivity of membrane has been remarkably improved by the plasma
treatment. The selectivity and the permeation rate of CO2/CH4
obtained were 53 and 3.3×10-4 cm3/s.cm2. cmHg.
3.1.2 Polyacetylenes
Table 3. Permeability coefficients and
selectivities for CO2/CH4 in substituted polyacetylenes
No. (-CR=CR'-)n
R
R' |
Permeability
coefficient, P×1010
[cm3(STP).cm/s.cm2.
cmHg]
CO2
CH4 |
Selectivity
CO2/CH4 |
With bulky
substitute
1 Me SiMe3
2 H t-Bu
3 Me SiMe2CH2SiMe3
4 Me SiMe2CH2CH2SiMe3
5 H o-C6H4SiMe3
6 H o-C6H4CF3
With long n-alkyl group
7 Me n-C7H15
8 Cl n-C8H17
9 Cl n-C6H13
10 Cl n-C4H9
11 Me SiMe2-n-C6H13
12 H CH(n-C5H11)SiMe3
13 H CH(n-C3H7)SiMe2-n-C6H13
With phenyl group
14 Ph Me
15 Ph Et
16 Ph n-C6H13
17 Ph Cl
18 H o-C6H4Me
19 H CH(n-C3H7)SiMe2Ph |
19000
560
310
150
290
130
130
170
130
180
71
120
70
25
40
48
23
15
54 |
4300
85
45
28
38
6.6
40
46
33
30
13
21
17
2.8
4.4
14
1.3
3.0
7.0 |
4.4
6.6
6.9
5.3
7.6
19.6
3.3
3.7
3.9
6.0
5.5
5.7
4.1
8.9
9.1
3.4
17.1
5
7.7 |
Poly[1-(trimethylsilyl)-1-propane], [-CH3C=CSi(CH3)3-]n,
designated hereafter PTMSP, has the highest intrinsic gas permeability of all synthetic
polymers known at present.[46] Although it is a glassy polymer (Tg>200°C),
was found to have an approximately ten-fold higher permeability for light gases than
rubbery PDMS, but a somewhat lower selectivity.
The exceptionally high permeability of PTMSP has been attributed to its
large free volume, which was believe to arise from the PTMSP matrix consists of relatively
stiff backbone chains separate by bulky trimethylsilyl side groups, Si(CH3)3.
The stiffness of the backbone chains is due in part to the alternating double bonds of the
polymer and in part to the fact that the bulky trimethylsilyl groups hinder intrasegmental
rotation. These groups also prevent chain packing by serving as "intersegmental
spacers".
In order to study the
structure/permeability relationships of these polymers and discover polymer structure that
exhibit a substantially higher gas selectivity than PTMSP without a significant decline in
the permeability, a large number of substituted polyacetylenes have been synthesized.[47,
48] Some of the results are presented in Table 3.[49]
Because the rates of gas permeation through PTMSP
decrease markedly with time or on thermal cycling, and their gas selectivities low, no
practical uses of the polyacetylenes as membrane materials have been found so far.
3.1.3 Poly(vinyltrimethylsilane)
Poly(vinyltrimethylsilane), designated hereafter PVTMS, [-CH2CHSi(CH3)3-]n,
is another glassy polymer which exhibits a high gas permeability (as shown in Table 1) due
to its bulky trimethylsilyl pendant groups, as is the case also for PTMSP.[50]
The main difference between these two polymers lies in that PVTMS has flexible vinyl
backbone chains whereas PTMSP has stiff backbone chains with alternating doublebonds. The
gas permeability of PVTMS is 1-3 orders of magnitude lower than that of PTMSP, but the gas
selectivity of PVTMS is markedly higher than that of PTMSP. Now PVTMS membranes have been
used in Russia to produce oxygen-enriched air for oxygen therapy. But this material for
gas separation appears to have received relatively little attention in the west.
3.2 Improvement of the permeability of polymers with high selectivity
3.2.1 Polyimide
Polyimides have been identified as materials with high selectivities for CO2/CH4
(over 60-80). In addition to high selectivity, polyimides have high glass transition
temperature(Tg>300°C) and can, therefore, be used at high service
temperatures. A substantial insight has been gained in the last ten years into the effects
of variations in the chemical structure of polyimides on gas solution and transport in
these polymers. As a result, polyimides exhibiting increasingly higher gas selectivities
and permeabilities are being developed in academic and industrial laboratories. In
particular, those polyimides with a hexafluoro substitute carbon -C(CF3)2
in the backbone have been found to be considerably more CO2-selective than
other glassy polymers with comparable permabilities.[51-60] A family of
polyimides and related materials are used by DuPont and Ube for commercial gas separation
membranes.Table 4 lists the permeability coefficients and selectivities of CO2/CH4
in the several excellent polyimides known as far.
Table 4. Permeabilities and selectivities of
CO2/CH4 in polyimides* [51-60]
|
Permeability
coefficient, P×1010
[cm3(STP). cm/s. cm2.
cmHg]
CO2
CH4 |
Overall
selectivity
CO2/CH4 |
6FDA-ODA
6FDA-MDA
6FDA-IPDA
6FDA-6FpDA
6FDA-m-DDS dense
asymmetric
6FDA-DMMDA
HQDPA-DMMDA |
23.0
24.2
30.0
63.9
3.2
69.0
17.0
1.7 |
0.38
0.43
0.70
1.60
0.028
0.51
0.29
0.021 |
60.5
56.3
42.9
39.9
116
136
59.4
79.4 |
*6FDA:2,2-bis(3,4-dicarboxyphenyl) hexafluoro
isopropane dianhydride
ODA:oxydianiline
MDA:methylenedianiline
IPDA:isopropylidenedianiline
PDA:phenylenediamine
DDS:diaminodiphenylsulfone
DMMDA:3,3'-dimethyl-4,4'-methylene dianiline
HQDPA:1,4-bis(3,4-dicarboxyphenyl) benzene dianhydride
To reduce undesirable effects
caused by CO2 induced swelling in CO2/CH4 separation
processes, the polyimide structure was stabilized with crosslinks. One method for
crosslinking membrane materials is the UV-irradiation of benzophenone-containing
polyimides or bisphenol A based polyacrylates.[61, 62] This leads, especially
in the separation of gas pairs with a large difference in molecular size, to a significant
improvement of permselectivity. But simultaneously the permeability is decreased by
crosslinking due to the strongly reduced chain mobility is decreased packing density of
the polymer chains. A disadvantage of photochemical crosslinked membrane materials is that
the degree of crosslinking depends strongly on experimental conditions, i.e. irradiation
time or the type of mercury lamp. Moreover, under the experimental conditions of
UV-irradiation crosslinking reaction as well as photo-fries rearrangements are possible.[62]
Claudia et al. synthesized polyimides with strong polar
associating functional groups as well as chemical crosslinked polyimides and copolyimides
with simultaneous inhibition of chain mobility and intrasegmental packing by changes in
backbone structure.[63] In the polymerization reaction 6FDA was used as
dianhydride monomer and mPD(m-phenylene diamine) and DABA (diamine benzoic acid) were used
as diamine monomers. With copolyimides containing strong polar carboxylic acid groups
(i.e. 6FDA-mPD/DABA 9:1) reduced plasticization was seen up to a pure CO2 can
be reduced at least up to a pure CO2 feed pressure of 35atm. With increasing
degree of crosslinking, increasing CO2/CH4 selectivity was found
because of reduced swelling and polymer chain mobility. By using ethylene glycol as a
crosslingking agent, CO2 permeability was not significantly lower because the
reduced chain mobility was compensated by the additional free volume caused by the
crosslinks.
3.2.2 Polyaniline
Polyaniline, (C6H4NH)n, has attracted considerable
attention because of the surprisingly high gas selectivity.[64-66] Anderson
et.al reported that a remarkable selectivity of CO2/CH4 in
polyaniline, 336, was achieved by a complex process involving doping, undoping, and
redoping membranes made from this polymer with select counterions, like acid solution of
HF, HCl, HBr and HI. This report shows that conjugated polymer is one of the most exciting
materials for gas separation membranes.[64]
Hachisuka et al. used an oxidized polyaniline as undoped
film, use various protonic acids, e.g., methane sulphonic acid, polyvinyl sulphonic acid,
polyisoprene sulphonic acid, and polyvinyl sulfate as dopants. It has shown that CO2
permeability was increased by the formation of a quinonediimine unit in polyaniline with
the oxidation. The selectivity of polyaniline membranes was found to be remarkably
improved by doping. In particular, the selectivity of the polyaniline membrane for CO2/CH4
doped with polyvinyl sulphonic acid as a polymer dopant went up to over 2000. Table 5 show
the selectivity of CO2/CH4 in polyaniline membranes doped with
various dopants.[65]
Table 5. Permeabilities and selectivities of
CO2/CH4 in polyaniline
Dopant |
Permeability
coefficient, P×1010
[cm3(STP). cm/s. cm2.
cmHg]
CO2 |
Overall
selectivity
CO2/CH4 |
Polyvinyl
sulphonic acid
Polyvinyl sulfate
Polyisoprene sulphonic acid
HCl
Methane sulphonic acid
no |
0.029
0.012
0.023
0.0027
0.015
0.079-0.14 |
2200
250
400
430
200
59-37 |
3.2.3 Polytriazoles and polyoxadiazoles
These polymers have been stated to be chemically resistant as well as thermally stable
with glass transition temperature between 260 and 360°C. Gebben et al. have measured the
permeability of poly[1,3-phenyl-1,4-phenyl]-4-phenyl-1,3,4-triazole] (TIPT) to CO2
and CH4 at the temperatures up to 200°C.[35] Its selectivity with a
CO2/CH4 mixture containing 20mol% CO2 at 25°C is over
60, a CO2 permeability is 10-20Barrer. The Tg of 270°C of TIPT is
lower than that of a number of polyimides with comparable selectivities to CO2/CH4
gas pair. This suggests that the intrasegmental mobility of TIPT is higher than that of
the latter polymers, perhaps due to the mobility of the phenyl rings in the para
positions. The high selectivity of TIPT to CO2/CH4 gas pairs is
unexpected in view of its relatively large fractional free volume (FFV) and moderate Tg.
A sharper free-volume distribution in TIPT any conceivably account for the gas selectivity
of TIPT.
An unusually high CO2/CH4 selectivity of 168, at
an unspecified temperature, has been reported for a poly(1,3,4-oxadiazole)(POD) which
incorporates a diphenyl ether (DPE) moiety in its backbone chains.[64] However,
the permeability of this polymer to CO2 is very low, 0.3 Barrer. The high Tg
of DPE-POD of 333°C indicates a low intrasegmental mobility, i.e., a high backbone-chain
stiffness, in spite of the presence of potentially mobile -O- linkages in the DPE moiety.
The very high CO2/CH4 selectivity and low permeability to CO2
suggest a high chain packing density and low FFV, and possible a narrow free-volume
distribution. Rotation around -O- linkages is probably inhibited by the high chain
packing.
By contrast, substitution in POD of either
1,1,3-trimethyl-3-phenylindane (PIDA) or 4,4',2,2'-diphenyl hexafluoropropane (HF) yielded
polymers with much higher permeabilities to CO2, 78-93 Barrer, but relatively
low CO2/CH4 selectivities of 26-28.
3.3 Polymer blending
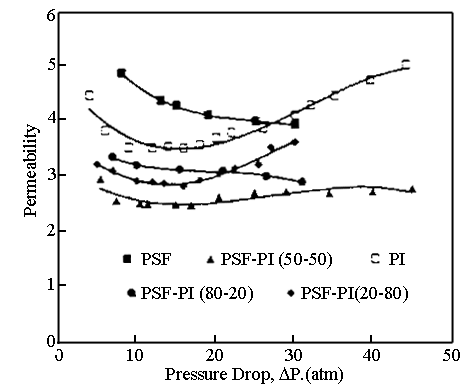
Fig. 7 Permeability of CO2
for various PSF/PI blends at 40°C
Although polyimide show excellent mechanical
properties, high temperature and chemical resistance, and separation performances for CO2,
the polyimides are seriously affected by highly soluble penetrants CO2, which
above a given partial pressure can plasticize the polymer matrix.[68] The
critical partial pressure of plasticization for polyimide is relatively low, varying
between 10-20 bar.[69] For this reason polyimide membranes have found little
application in the separation of CO2 from light hydrocarbons in enhanced oil
recovery or in landfill gas upgrading programs.
Polymer blending has been taken as optimization of membrane properties.
If one could achieve equivalent segmental composition by either blending or
copolymerization, it is currently thought that equivalent solution/diffusion separation
properties would result. Although earlier extensive work on polymer blend membranes was
attempted to do, it is very difficult to find miscible polymer blends with satisfied
separation performances.[33, 34]
However, Sakellaropoulos et al. prepared the blend membrane
from the mixtures of the polysulfone and the aromatic polyimide.[69, 70]
Because the critical pressure of plasticization for polysulfone exceed 55Bar, blend
membranes were considerably more resistant to the plasticization phenomenon compared with
those of pure polyimide, shown as in Fig. 7.[71] In addition, the membranes
showed significant permeability improvements, compared to pure polyimide, with minor
change in their selectivity. Polysulfone and polyimide proved to be completely miscible
polymers as confirmed from optical microscopy, glass transition temperatures and
spectroscopy analyses of the prepared mixtures. The complete miscibility permits the
preparation of symmetric and asymmetric blend membranes in any proportion (1-99%) of
polysulfone and polyimide.
Blending of suitably selected polymers is generally considered as a
viable method to modify the properties of polymers used for preparation of gas separation
membranes. But the candidate polymer pairs for preparation of miscible blends are few.
3.4 Organic-inorganic hybrid membranes
Table 6. Permeabilities and selectivities of
CO2/CH4 in the 6FPAI and 6FPAI/TiO2
|
Permeability
coefficient, P×1010
[cm3(STP). cm/s. cm2 .
cmHg]
CO2
CH4 |
Overall
selectivity
CO2/CH4 |
6FPAI
6FPAI/TiO2 |
52.7
44.7 |
1.80
1.3 |
29.3
34.4 |
Because of the limitations of purely organic
polymers, especially to plasticization, organic-inorganic hybrid materials may offer new
possibilities to gas separation application.[35, 72] Hybrid organic-inorganic
materials can be formed utilizing a sol-gel process via a number of approaches. One method
involves treating an orthosilicate directly with the organic polymer or an oligomer, which
contains functional groups capable of a cross-reaction with the inorganic oxide, thus
provide connectivity between the organic phase and inorganic network.[73]
Alternatively, alkoxysilane monomers with a polymerizable organic moiety covalently
attached to the silicon can be precipitated, followed by polymerization of the organic
moiety.[72] Finally, in situ polymerization of the alkoxide within a swollen
polymer network can be used to form nano- or micro composite materials without covalent
crosslinks.[72]
Hu et al. have successfully fabricated a fluorinated
poly(amide-imide)/TiO2 nano-composite membranes by a sol-gel method. The
nano-composite membrane has a denser and a more rigid structure compared to the
corresponding pure poly(amide-imide) membrane. Furthermore, there appear to be specific
intermolecular interactions between CO2 and the TiO2 domains.
Finally, the composite membrane has shown higher permselectivities for CO2/CH4,
as shown in Table 6, even at very low volume concentration of the TiO2
component. Such results are encouraging, because they suggest that possibly higher
selectivities could be achieved at increasingly higher concentrations of the ceramic
component.
4 CURRENT PROBLEMS AND RESEARCH TOPICS IN
FUTURE
These "tailor-made" polymers allow both higher selectivities of CO2/CH4
and higher permeabilities of CO2 compared to the traditional polymers. Although
a very substantial amount of data on the solution, diffusion, and permeation of CO2/CH4
in a variety of rubbery and glassy polymers was already available, the relationships
between the chemical structure of polymers and their gas permeability and selectivity were
only poorly understood. The new polymers with good gas selectivity or permeability, like
6FDA-ODA, polyaniline, PTMSP and PDMS etc., was occasionally synthesized or found. But it
is largely based on prior experience and considerable trial and error. And these
"tailor-made" polymers themselves exist some problems for CO2-selective
separation processes. Polyimide is sensitive to plasticize by CO2. Polyaniline
with highest selectivity for CO2/CH4 known so far is not
sufficiently stable in the presence of humidity, prolonged oxygen exposure and physical
aging.
Systematic primary chemical structure modificatioin of the polymer
backbone which simultaneously increase chain rigidity and decrease chain packing density
have been shown to lead to membranes with improved permeability without significant losses
in gas permselectivity. But as chain rigidity increases, it becomes more difficult to find
acceptable solvents in which to dissolve the material. Some of the lower free volume
imides must also be cast in amide acid form followed by thermal ring closure. Some such
materials, in fact are used in commercial membranes; however, they are clearly more
complex and expensive.
A large increase in solubility might induce plasticization, which would
decrease membrane permselectivity. Another deleterious effect of strong polymer-penetrant
interactions is the loss of mobility selectivity due to excessive binding between the gas
and the polymer. Clearly, the strategy of augmenting permselectivity by increasing
solubility selectivity is a delicate balance. An increase in polymer polarity with a
simultaneous increase polymer free volume might be expected to increase CO2/CH4
solubility selectivity, permeability and permselectivity. However, studies involving the
introduction of substitutents, which simultaneously interact with one component in a gas
mixture and frustrate chain packing have not been reported.
From a practical standpoint of processing advance materials, most
current generation commercial membranes have asymmetric forms with an open porous support
on top of which is an integral skin formed during the cast of a solution of the polymer
into a nonsolvent bath. Besides high permeability and selectivity values, processability
of the membrane material into desired membrane morphology is of utmost importance.
In extreme cases, the gaseous feed stream can be composed of over 50%
CO2 at an elevated temperature and up to a feed pressure of 60atm. These
extreme operation conditions result in the swelling and plasticization of most membrane
materials by the CO2 present in the feed stream. For the application of
membrane based gas separation in EOR processes, it is important to develop new membrane
materials with reduced plasticization effects due to higher CO2 partial
pressure.
Materials research on membranes for CO2/CH4 will
fouse on these two fields: (a) development of new polymer membrane materials with improved
selectivities and permeabilities, simultaneously with unplasticization to higher pressure
of CO2. (b) fabrication of new membrane morphologies allowing higher
fluxes(e.g., asymmetric membranes, hollow fiber membranes, and composite membranes) for a
given polymer with high permeability of CO2 and high selectivity of CO2/CH4.
REFERENCES
[1] Hao J H. The preparation of Integrally-skinned asymmetric
membrane for separation of CO2/CH4 and studies on its formation
mechanism, PhD Dissertation, Tianjin University, 1995.
[2] Schell W J. CEP, 1982, 78: 45.
[3] David P. Oil & Gas Journal, Technology, 1984: 85.
[4] Goddin C S. Hydrocarbon Processing, 1982, 61 (5): 125.
[5] Bhide B D, Stern S A. J. Membrane Sci., 1993, 81: 209.
[6] Cooley T E, Dethlff W L. Chem. Eng. Progress, 1985, 81: 45.
[7] Fournie F J C, Agostini T P. J. Petroleum Tech., 1987, 39: 707.
[8] Mc Kee R L, Changela M K, Reading G J. Hydrocarbon Processing, 1991, 70 (4): 63.
[9] Maddox R N, Morgan D J. Hydrocarbon Processing, 1986, 64 (8): 59.
[10] Babcoek R E, Spillman R W, Goddin G S et al. Energy Progress, 1988, 8 (3): 135.
[11] Schell W J. J. Membrane Sci. 1985, 22: 217.
[12] Vansant E F, Dewolfs R. Gas Separation Technology. Amsterdam: Elsevier Science
Publishers B. V., 1990: 457.
[13] Rautenbach R, Welsch K J. membrane Sci., 1994, 87 (1): 107.
[14] Cecille L, Toussaint J C. Future Industrial Prospects of Membrane Processes, New
York: Elsevier, 1989.
[15] Koros W J, Fleming G K. J. Membrane Sci., 1993, 83 (1): 1-80.
[16] Bhide B D, Stern S A. J. Membrane Sci., 1993, 81 (3): 238.
[17] Teramoto M, Nakai K, Ohnishi N et al. Ind. Eng. Chem. Res. 1996, 35 (2): 538-45.
[18] Koros W J, Fleming G K, Jordan S M et al. Prog. Polym. Sci., 1988, 13: 339-401.
[19] LeBlanc O H, Ward W J, Matson S L et al. J. Membrane Sci., 1980, 6: 339-343.
[20] Weinkauf D H, Paul D R. in Barrier Polymers and Barrier Structures, W. J. Koros, ed.,
American chemical Society, 1990.
[21] Koros W J, Hellums M W. Encyclopedia of polymer Science, 2nd edn., New
York:Wiley-Interscience Publishers, Supplement Volume, 1989: 724.
[22] Ghosal K, Freeman B D. Polymers for Advanced Technologies, 1994, 5: 673-697.
[23] Chern R T, Koros W J, Hopfenberg H B. Material Science of Synthetic membranes, D. R.
Lloyd, ed., Washington, DC: American Chemical Society, 1985: Chapter 2.
[24] Chern R T, Brown N F. Macromolecules, 1990, 23: 2370.
[25] van Amerongen G J. J. Polym. Sci., 1950, 5: 307.
[26] Pilato L, Litz L, Hargitay B et al. Polym. Preprint, Am. Chem. Soc. Div. Polym. Sci.,
1950, 5: 307.
[27] Koros W J. J. Polym. Sci.:Polym. Phys. Ed., 1985, 23: 1611.
[28] Ghosal K, Chern R T, Freeman B D et al. J. Polym. Sci., Part B: Polym. Phys. 1995, 33
(4): 657-66.
[29] Chern R T, Provan C N. Macromolecules, 1991, 24: 2203.
[30] Stam H. Future Industrial Prospects of Membrane Processes, Ed. By Lecille L and
Toussaint J C, NY: Elsevier, 1989.
[31] Kesting R E, Fritzsche A K, Murphy M K et al. J. Applied Polym. Sci., 1990, 40: 1557.
[32] Barbari T A, Datwani S S. J. Membrane Sci., 1995, 107: 263-266.
[33] Paul D R. Polymer Compatibility and Incompatibility: Principle and Practice, K. Solc
Ed., MMI Press Symp. Ser., 2, New York: Harwood Academic Publishers, 1982.
[34] Chiou J S, Paul D R. J. Appl. Polym. Sci., 1987, 33: 2935.
[35] Gebben B, Mulder N H V, Smolders C A. J. Membrane Sci., 1989, 46: 29-41.
[36] Li Y, Ding M, Xu J. Polymer International, 1997, 42 (1): 121-126.
[37] Hu Q, Marand E, Dhingra S et al. J. Membrane Sci., 1997, 135: 5-79.
[38] Hensema E R. Adv. Mater., 1994, 6 (4): 269-279.
[39] Pye D G, Hoehn M H, Panar M. J. Applied Polym. Sci., 1976, 20: 287-301.
[40] Hoehn H H. Material Science of Synthetic membranes, D. R. Lloyd, ed., Washington, DC:
American Chemical Society, 1985: 81-98.
[41] Stern S A, Shah V M, Hardy B J. J. Polym. Sci., Part B: Polym. Phys., 1987, 25:
1263-1298.
[42] Shah V M, Hardy B J, Stern S A. J. Polym. Sci., Part B: Polym. Phys., 1986, 24:
2033-2047.
[43] Ashworth A J, Brisdon B J, England R et al. Br. Polym. J., 1989, 21: 491.
[44] Ashworth A J, Brisdon B J, England R et al. J. Membrane Sci., 1991, 56: 217.
[45] Matsuyama H, Teramoto M, Hirai K. J. Membrane Sci., 1995, 99: 139-147.
[46] Masuda T, Isobe E, Higashimura T. J. Am. Chem. Soc., 1983, 105: 7473-7474.
[47] Takada K, Matsuya H, Masuda T et al. J. Applied Polym. Sci., 1985, 30: 1605-1616.
[48] Masuda T, Iguchi T, Tang B Z. Polymer, 1988, 29: 2141-2149.
[49] Odani H, Masuda T. Design of polymer membranes for gas separation, in N.
Toshima(Ed.), New York, NY, 1992, 107-144.
[50] Davydova M B, Yampol'skii Yu P, Durgar'jan S G. Poly. Sci. USSR, 1988, 30: 1501-1507.
[51] O'Brien K C, Koros W J, Husk G R. J. Membrane Sci., 1988, 35: 217-230.
[52] Kim T H, Koros W J, Husk G R et al. J. Membrane Sci., 1988, 37: 45-62.
[53] Stern S A, Mi Y, Yamamoto H et al. J. Polym. Sci., Polym. Phys. Ed., 1989, 27:
1887-1909.
[54] Tanaka K, Kita H, Okano M et al. Polymer, 1992, 33: 585-592.
[55] Matsumoto K, Xu P. J. Membrane Sci., 1993, 81: 23-30.
[56] Tanaka K, Kita H, Okamoto K. J. Polym. Sci., Part B: Polym. Phys., 1993, 31:
1127-1133.
[57] Kawakami H. J. Applied Polym. Sci., 1996, 62: 965-971.
[58] Rene A, Canada, CA2133046, 1995.
[59] Hiroyoshi K, Masato M, Shoji N. J. Applied Polm. Sci., 1996, 62 (7): 965-970.
[60] Hiroyoshi K, Masato M, Shoji N. J. Membrane Sci., 1996, 118 (2): 223-230.
[61] Kita H, Inada T, Tanaka K et al. J. Membrane Sci., 1994, 87: 139.
[62] Wright C T, Paul D R. J. Membrane Sci., 1997, 124: 161 .
[63] Staudt-Bickel C, Koros W J. J. Membrane Sci., 1999, 155 (1): 145-154.
[64] Anderson M R, Mattes B R, Reiss H et al. Science, 1991, 252: 1412-1415.
[65] Hachisuka H, Ohara T, Ikeda K I et al. J. Applied Polym. Sci., 1995, 56: 1479-1485.
[66] Chang M J, Liao Y H, Myerson A S et al. J. Applied Polym. Sci., 1996, 62 (9):
1427-1436.
[67] Hensema E R, Ph.D. Dissertation, University of Twenty, Enschede, 1991.
[68] Koros W J, Coleman M R, Walker D R B, Ann. Rev. Sci., 1992, 22: 47.
[69] Sakellaropoulos G P, Kaldis S P, Kapantaidakis G C et al. European patent, EP 778077,
1997.
[70] Kapantaidakis G C, Kaaldis S P, Dabou X S et al. J. Membrane Sci., 1996, 110:
239-247.
[71] Sander E S, Jordan S M, Sabrmanian R. J. Membrane Sci., 1992, 74: 29.
[72] Okazaki I, Ohya H, Semenova S I et al. J. Membrane Sci., 1998, 141 (1): 65-78.
[73] Smaihi M, Jermoumi T, Marigan J et al. J. Membrane Sci., 1996, 116: 211-220.
|