Effect of post-treatment on the
performance of the particle-filled PAN membrane
Ge Jijun, Yin Yan, Cui Yongfang , Zhang
Zhiying, Zhou Hua
(Department of Material Science, Tianjin Institute of Textile Science and Technology,
Tianjin, 300160, China)
Received Dec. 15, 1999
Abstract The post-treatment process of
matrix PAN/SiO2 (PAN, Polyacrylonitrile) and its influence on the membrane
performance are studied. The results show that the post-treated composite increases the
heat-resistance. The post-treated flat membrane maintains higher flux without decreasing
the retention.
Key words Polyacrylonitrile, particle-filled membrane, dynamic viscoelastic
properties, water permeability
The polyacrylonitrile membrane has long
been used as flat or hollow fiber. It is also used as layers of composite membrane because
of its excellent capability to resist pollution and chemical reactions. Because of the
porous and low glass transition temperature in wet condition, the membrane will shrink
during dewatering or heating unless they are treated with special chemical or physical
method[1]. Since most of the composite processes are carried out in a dry state
at a high temperature, it is impossible to use the deformed membranes as matrix. A few
articles about PAN matrix and its post-treatment are reported[2-5] , but some
of them deal with SiO2 reinforcement. In order to overcome the disadvantage of
"the membrane densification" in making composite
membrane, the membrane matrix of PAN/SiO2 and its post-treatment are studied.
The result shows that post-treated PAN/SiO2 can increase the ability of
heat-resistance without deformation and loss of their performance.
1 RIMENTAL
1.1 Materials
The PAN (=30,000) is obtained from Qinhuangdao Factory of acrylon. Silica (used for
chromatography) is imported from Germany.
1.2 Sample preparation
An amount of PAN is dissolved in DMF to form an 18%(wt.) solution. Then SiO2
is put into the solution and the solution of PAN/SiO2 is rapidly agitated for
at least 3 hours. The solution is casted on glass and coagulated in water at 25°C to form a smooth membrane. The membranes are kept in water for use.
The draw and the heat treatment of membranes are carried out in boiling water
respectively.
1.3 Instrumentation
The morphology of the membrane is scanned with a Hitachi S-450 scanning electron
microscope. The dynamic viscoelastic curves are measured on a Rheovibron DDV-II-EA. Water
flux and retention are evaluated with ultrafilter equipment made by Tianjin Institute of
Membrane Technology.
2 RESULTS AND DISCUSSIONS
2.1 Water flux and retention
The water flux increases markedly with the increase of draw ratio, as
shown in Fig. 1. The fixed length heat-treatment causes the flux to reduce to only half of
that of the untreated. But after the membranes are drawn, the water flux increases with
draw ratio. Provided that the draw ratio is 250%, the flux rises up to four times that of
the untreated one. Simultaneously, the retentions of the drawn membranes keep almost the
same as the undrawn one. For example, the post-treatment membranes are used to determine
the retention of ploy (ethylene glycol)(PEG, =10,000) and the results are listed in Table
1.
Fig.1 Relationship between draw ratio and flux
Table 1 The PEG retention of post-treatment membranes
Treatment
Conditions |
Untreated |
Fixed length heated |
Drawn 150%
heated |
Drawn 200%
heated |
Drawn 250%
heated |
Retention |
99.0% |
98.7% |
98.9% |
99.0% |
99.1% |
2.2 Morphology
The surfaces of drawn membranes are observed by scanning electron microscope, as shown
in Fig.2. The shapes of the surface pores of particle-filled PAN membranes are altered
from round to ellipse. Inside the pores, there are some particles, which divide one pore
into two. A great many of hypopores appear on the surface. The drawn membranes have a more
porous area than that of the undrawn one. But the average size of a pore does not alter
remarkably. This is why the drawn membranes have higher flux and remain constant
retention.
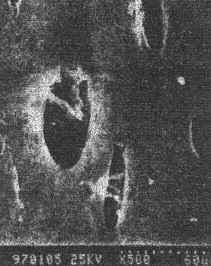 |
Fig.2 SEM micrograph of surface of
PAN/SiO2 membrane with draw ratio of 2.24 |
2.3 Dimension stability
The untreated membranes are noticeably warped and become brittle in dry condition.
This makes the membrane unfit for use. The effects of treatment temperature and draw ratio
on the dimension stability of dry membranes are shown in Table 2.
Table 2 The effects of heat treatment and draw ratio on dimension stability
Treatment
Temperature |
Fixed length
heated |
Drawn 150%
heated |
Drawn 200%
heated |
Drawn 250%
heated |
30°C |
Smooth, brittle |
Smooth, brittle |
Smooth,
flexible |
Smooth, good
flexible |
40°C |
Smooth, brittle |
Smooth, brittle |
Smooth, flexible |
Smooth, good flexible |
60°C |
Lightly warped, brittle |
Little warped,
brittle |
Smooth, flexible |
Smooth, good flexible |
80°C |
Warped, brittle |
Warped, brittle |
Lightly warped, flexible |
Smooth, good flexible |
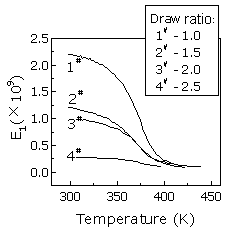 Fig.3 The effect of the post-treatment on the elastic
modulus.
It can be seen that the membranes become more stable and flexible with
the increase of the draw ratio. In order to explain the increase of dimension stability
with draw ratio, the dynamic viscoelastic experiments are carried out and the results are
shown in Fig. 3.
This indicates that the elastic module of the membrane decreases with
the increase of the draw ratio below the temperature of 400K. The smaller the draw ratio
is, the more quickly the elastic modules of the membrane drop with the rise of the
temperature. With a draw ratio of 250 %, the modules change slightly, which means that it
is not sensitive to temperature. So, the drawn membranes possess more dimension stability
in higher temperature, even at 80°C(see Table 2).
3 CONCLUSION
The dimension stability of the membrane of PAN/SiO2 in dry conditions can
be greatly improved by means of drawing and heating treatment.
REFERENCES
[1] Craig R, Bartels K K, Wachtel A. J. Membr. Sci., 1987, 32: 291-321.
[2] Yang M C, Chou M T. J. Membr. Sci., 1996, 116: 279.
[3] Cui Y F, Lin D S, Zhao Y H et al. Water Proc. Tech., 1993, 13: 19-24.
[4] Watanabe K, Kyo S. J. Chem. Eng. Jpn., 1993, 1: 17-21.
[5] Heintx W S. J. Membr. Sci., 1994, 89: 153.
|