Study of microwave effect in some
polymerization
Lu Jianmei, Ji Shunjun, Wu Jianfei, Zhu
Xiulin
(Department of Chemistry and Chemical Engineering, Suzhou University, Jiangsu
215006,China)
Received Feb. 25, 2001; Supported by the
National Natural Science Foundation of China (No.20076031).
Abstract The microwave irradiation
polymerization of the dibutyltin maleate (DBTM) and allyl thiourea (AT) system[1]
or the DBTM and stearic acid vinyl ester (SAVE) system[2] showed that the
copolymerization can go on wheels by microwave irradiation whereas there is no polymer
formed by thermal polymerization at the same temperature in 7h. It may be not only the
simple dielectric heating but also the "the microwave
effect". In order to verify the effect of microwave, eight
systems were selected for investigation to compare their thermal polymerization with the
microwave polymerization.
Keywords thermal effect, microwave effect, microwave irradiation, thermal
polymerization
Microwave ovens have been used in chemical
laboratories for moisture analysis [3] and wet ashing procedures of biological
and geological materials [4] for a number of years. In recent years, microwave
irradiation was widely used in the chemical field [5,6]. In organic
chemistry, the use of microwave heating results in short reaction time compared with
conventional heating [5,7], ease of workup after a reaction. Microwave ovens
provide a clean and cheap alternative to conventional oil baths. The microwave irradiation
was also used in the polymerization reactions recently [8]. In the field of
synthetic polymer chemistry, microwave energy has been utilized for the radical
polymerization of vinyl monomers such as 2-hydroxy ethyl methacrylate[9],
methyl methacrylate (MMA)[10], and styrene[11], during the course of
our studies, we have already reported the microwave irradiation solid state
copolymerization in binary maleic anhydride and dibenzyl maleate system[12],
maleic anhydride (MAH) and AT system in solid state[13], on the other hand, the
curing of polymer such as eposxy resins and polyurethane[14], as well as the
imidization of polyamic acids (PAA)[15] has also been studied under microwave
irradiation. However the mechanism of their homo-polymerizations or copolymerizations
under microwave irradiation is still need to be studied. Here, the effect of microwave
irradiation on some monomers for their copolymerizations was studied. In comparison with
conventional copolymerization, microwave irradiation obviously had decisive function in
the copolymerization, e.g. some copolymerization reactions occurred easily, and the
inherent viscosity was greater either and it also showed that the microwave not only had
thermal effect, but also had more important nonthermal effect. The reasons of nothermal
effect were also discussed. This work also provides a new approach to studying
copolymerization.
1. EXPERIMENT SECTION
1.1 Base material
Stearic acid vinyl ester (SAVE) , analytical reagent; allyl thiourea(AT),
acrylamide (AM), itaconic acid (IA), maleic anhydride, N,N- methylene biacryamide (NBA),
dibutyltin maleate(DBTM), chemically pure; sodium acrylate (AANa), self-made by acrylic
acid.
1.2 Procedure of polymerization
1.2.1 Solid-phase polymerization under microwave irradiation
Solid-phase polymerization under microwave irradiation
was conducted in a special vial, the monomer(note 1) was degassed with N2 for 30 minutes,and the same original temperature was
required. The mixed monomers reacted at the optimum temperature (note 2) while adopting
intermittent irradiation, keeping under N2. After a certain time, the mixture
was poured into precipitating agent (note 3)
and the polymer was separated out. Filtering , washing, drying at lower temperature under
vacuum until constant weight. It was weighed and worked out the percent conversion of
polymerization.
[note 1]:The carrier was
ground with monomer together if the polymerization system contained it .
[note 2]:The optimum
temperature is the temperature closest to melting point of system while the monomer will
not melt.
[note 3]:Precipitating
agent for DBTM-SAVE system is ethyl acetate methanol solution about 1 : 1, for the other
polymerization systems is methanol .
1.2.2 Solution polymerization under microwave irradiation
The monomers were dissolved in a small quantity of DMF. The solution was poured
into reactor and was degassed under N2 for 30 minutes. The same original
temperature was required and the intermittent irradiation method was adopted. The
temperature of solution was controlled as the same as the one in 1.2.1 keeping under N2.
After a certain time, the mixture was poured into precipitating solvent and the polymer
was separated out. Filtering, washing, drying at lower temperature under vacuum until
constant weight. It was weighed and worked out the percent conversion of polymerization.
1.2.3 Conventional thermopolymerization
The monomers were ground thoroughly before setting into a special vial , degassed
under N2 for 30 minutes, set into the oven in which the temperature had been
set (the temperature is the same as the optimum temperature as before). It was heated for
7h. The final treatment was as before.
1.3 Measurement
1.3.1 Determination of inherent viscosity
The polymer inherent viscosity was determined by one-point method separately at 30.0±0.5℃,conditions as follows: DBTM AT system,inner diameter of U-viscometer is 0.35mm,chloroform-acetic acid solution 20:1;DBTM-SAVE system, the inner diameter is 0.7mm, benzyl
alcohol-chloroform solution 3:1.
1.3.2 Determination of reactivity ratio
The composition of the copolymer was determined by liquid chromatography (Shimadzu
model LC-6A. Chromatographic column condition: filler-spherisorb
CN 5m, size-4.0mm×150mm, velocity of flow-0.8ml/min).
The reactivity ratios were obtained by the Lewis and Mayo equation [1, 13,16].
2. RESULTS AND DISCUSSION
2.1. The copolymerization of DBTM and AT
2.1.1 Reactivity ratios of two monomers under microwave irradiation
The Lewis and Mayo composition equation is represented as follows:
(1)
M1 the concentration of AT in the system,
M2 the
concentration of DBTM in the system,
r1 reactivity
ratio of AT,
r2 reactivity ratio of DBTM.
If b = [M1] / [M2],a = d [M1] / d [ M2],then the equation (1) could be changed as:
or
(2)
Various composition of monomers (value of b ) were copolymerized by the
microwave (controlling conversion <10%). The relative value of "a" is
(3)
Here, [M1]0 and [M2]0 are the concentrations
of AT and DBTM respectively before reaction, which represents the compositions of
monomers. [M1] and [M2] are the concentrations of AT and DBTM
respectively after reaction, which were measured by liquid chromatography.
The line (Fig.1-Fig5) was obtained by (a-1)b/a as longitudinal
coordinates, b2 / a as horizontal ordinate. The
linear slope was r1,the linear intercept was -r2 . The detailed results
showed as Figure1 - 5 and Table 1.
Table 1 Reactivity ratio of
copolymerization system DBTM and AT *
|
solid phase
(no initiator,
no carrier) |
solid phase
(no carrier ,
initiator) |
solid phase
(no initiator,
SiO2 carrier) |
solid phase
(no initiator,
Al2O3 carrier) |
solution phase
(no carrier,
no initiator) |
rAT |
1.127 |
1.577 |
1.640 |
2.181 |
1.577 |
rDBTM |
0.102 |
0.364 |
0.262 |
0.417 |
0.364 |
initiator: 0.4% (wt) of
monomers, carrier: 160%(wt) of monomers
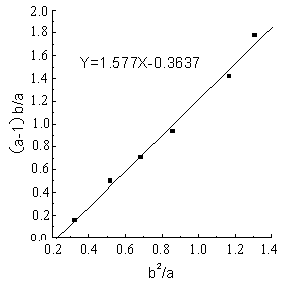
Fig.1 Solid phase and no
initiator, no carrier Fig.2 Solid
phase and no initiator, had carrier
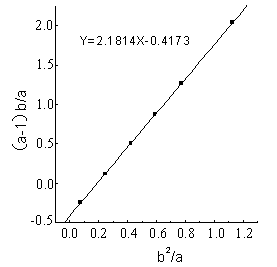
Fig.3 Solid phase and no
initiator, SiO2 as carrier Fig.4 Solid
phase and no initiator, Al2O3 as carrier
From the figures and table, the
results showed that in all of five reactions r1r2 <1,that was to say DBTM and AT were easy
to copolymerize under microwave irradiation, but the reactive ratio was different in a
wide range because of different polymerization systems.
2.1.2 The influence of the microwave irradiation energy
In the solid phase copolymerization of DBTM which has initiator or not, and intermittent
irradiation method was adopted, white polymer powder was obtained. The influence resulted
by the change of microwave irradiation energy showed as Figures 6, 7.
The power and the time of microwave irradiation are important operation
parameters. In this work, the influence of irradiation energy (product of power and time)
to the percent conversion and inherent viscosity of polymer was studied.
From the Figure 6, it can be seen that the percent conversion had an
increasing trend while the irradiation energy increased. This is identical to the free
radical polymerization mechanism, that is to say, when the irradiation power is certain,
the percent conversion increased with the increase of reaction time. At the same time,
when the irradiation energy is certain, the percent conversion in the system having
initiator is higher than that in the system having no initiator. It displayed that the
microwave irradiation can initiate the polymerization of this system, and the active
center of reaction system increased when the initiator was added, which resulted in the
increase of percent conversion.
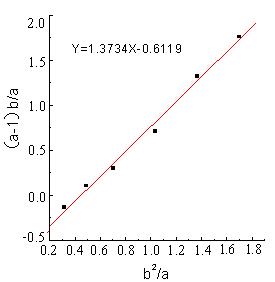 |
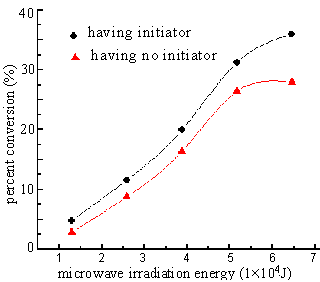 |
Fig.5 Solution
polymerization, no initiator
|
Fig.6 Relationship
between microwave irradiation energy and percent conversion
AT : DBTM = 1 : 1; initiator was 0.4%(wt) of monomers |

Fig.7 Relationship between microwave irradiation energy and inherent
viscosity of polymer
AT : DBTM = 1 : 1; initiator was 0.4%(wt)
of monomers
From the Figure 7, it can be seen that,the inherent viscosity had a decreasing trend while the microwave
irradiation energy increased, which was the same as the ordinary free radical
polymerization. On the one hand, because of the increasing of irradiation energy it
increased the chemical activity of chain free radical and resulted in the decreasing of
the molecular weight; and on the other hand, since there were no initiator and no solvent,the termination of chain radical may
be only coupled termination of diradical by itself. The microwave can cause the high speed
vibration of molecules, in other words, the chain radicals of system vibrate on high speed
too; the more of irradiation energy, the stronger the vibration is, and the chain radicals
collided with each other, the chance of coupled termination of diradical increased, the
molecular weight decreased.
The solution copolymerization of DBTM and AT under microwave
irradiation can also be carried out. The product was white powder.
2.1.3 Conventional copolymerization of DBTM and AT.
The experimental results showed that: when the system had no initiator, and the
solid-phase was heated for 7 hours, there was no any polymer formed; when the system had
initiator, there was only trace polymer formed. In comparison with conventional
copolymerization, microwave irradiation obviously had decisive function in the
copolymerization, and at the same time, it also showed that the microwave not only had
thermal effect , but also had more important nonthermal effect.
2.2 The copolymerization of SAVE and AM
The polymer was got after 2 minutes solid phase polymerization of SAVE and AM by
microwave. Although ,the polymer was also got after 12h heating polymerization at the same
temperature as microwave temperature 30°C, but the inherent
viscosity of this copolymer is less than the one of microwave polymerization.
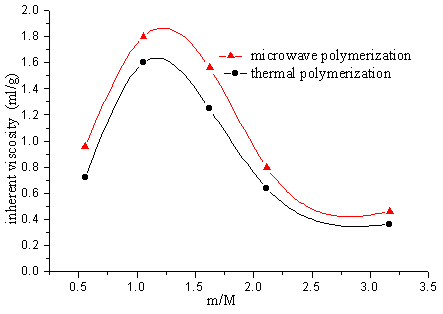
Fig.8 Relation
between polymer inherent viscosity and carrier quantity
m-carrier weight
M-total monomer weight
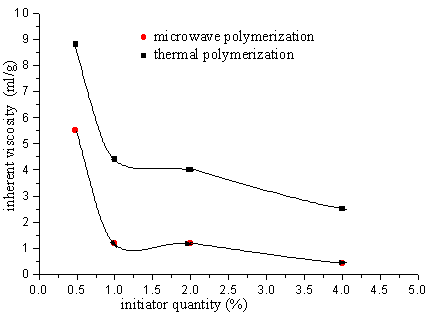
Fig.9 Relation between polymer inherent viscosity and initiator quantity
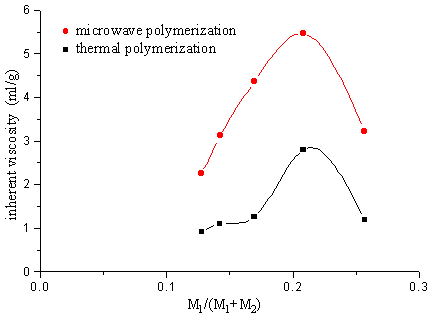
Fig.10 Relation between
polymer inherent viscosity and ratio of monomer
M1-AM
M2-SAVE
2.3 The copolymerization of SAVE and MAH
The polymer was obtained separately after 2 min. microwave irradiation or 12h thermal
polymerization of SAVE and MAH, but the inherent viscosity of the polymer by adopting
microwave irradiation is greater than the one by thermal polymerization.

Fig.11 Relation between polymer
inherent viscosity and ratio of monomer
M1-maleic, anhydride
M2-SAVE
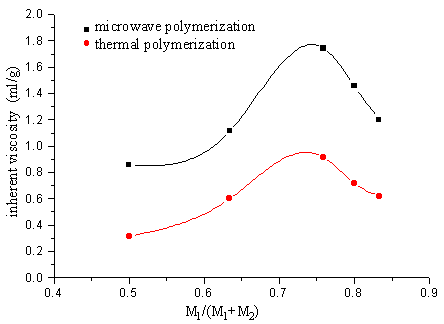
Fig.12 Relation between
polymer inherent viscosity and ratio of monomer in the presence of SiO2
carrier
M1-maleic, anhydride
M2-SAVE
2.4 The copolymerization of SAVE and IA
From the copolymerization of SAVE and IA the polymer prepared either after 2 minutes
microwave irradiation or 12h thermal polymerization, the inherent viscosity of the polymer
product by adopting microwave irradiation is greater than that one by thermal
polymerization.
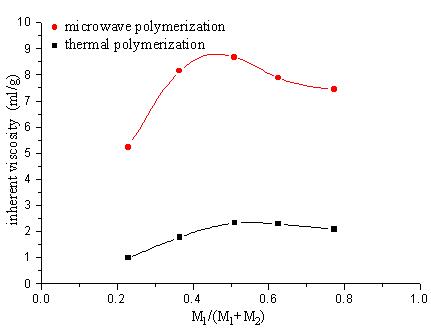
Fig.13 Relation
between polymer inherent viscosity and ratio of monomer
M1-IA M2-SAVE
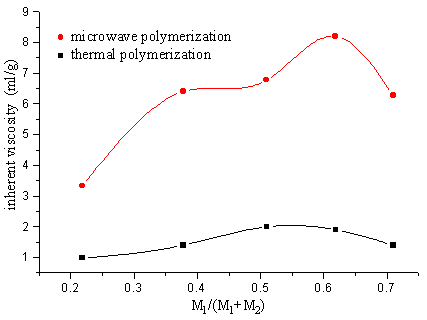
Fig.14 Relation between
polymer inherent viscosity and ratio of monomer on the presence of SiO2
carrier
M1-IA
M2-SAVE
2.5 Other systems as the following table
Table 2 Contrast between
microwave irradiation and thermal polymerization of other systems
System |
Microwave
irradiation |
Thermal
polymerization |
IA+AM |
2 minutes
polymer formed |
4 hours no
polymer |
AANa+NBA |
2 minutes
polymer formed |
4 hours no
polymer |
AM+MAH |
2 minutes
polymer formed |
4 hours no
polymer |
DBTM+SAVE |
2 minutes
polymer formed |
7 hours no
polymer |
3. CONCLUSION
From the systems studied, there is the special active effect of microwave nonthermal
effect besides the heating of dielectric.
The nonthermal effect comes into being because of three cases as follows probably:
3.1 The increasement of reaction rate because of the "overheat spot"
The overall temperature of mixture by microwave irradiation can not be looked as the
reaction condition[17,18]
, similarly to the “overheat spot”
of phonochemistry .The activity of microwave is due to the overheat spot formed by
dielectric relaxation within molecular size .that is to say ,the selective absorption of
active polar molecule to microwave picks up the reaction speed. While in the conventional
heat, the whole molecule must be heated before reaction.
3.2 The increasement of reaction rate because of the stirring effect
The microwave can make the molecular dipole of compound shift swiftly. The hindrances of
intermolecular bond to the rotate of dipole cause the dipole lag after electromagnetic
radiation. And it shows the reason why the thermal effect was observed after microwave
irradiation. This process can also be thought as molecular stirring or agitation. The
productive rates of the several researched reaction systems in this paper are all greater
than thermal polymerization. So high productive rate is the result of the stirring of
intramolecular dipole because of the increasing of temperature resulted by microwave. The
viewpoint that molecular stirring or agitation caused by the microwave is thought as the
nonthermal effect of microwave either.
3.3 The increasement of reaction rate because of the increasement of molecular
migration property
In the researched systems ,the slowest step of the solid phase reaction is the
interdiffusion process of reactant though the inert medium (Al2O3 or
SiO2). Since
the reaction rate depends on the slowest step, the enhancement of interdiffusion process
is important. At the same temperature, the microwave irradiation can strengthen the
interdiffusion property of reactants more easily than that in thermal reaction [19,20] .
REFERENCES
[1] Lu J M, Jiang Q S, Zhu X L et al. J. Appl. Polym. Sci., 2001, 79: 312.
[2] Lu J M, Jiang Q S, Zhu X L et al. Petrochemical Technology ( Shi You Hua Gong), 2000,
29 (10): 764.
[3] Hesek J A, Wilson R C. Anal. Chem., 1974, 46: 1160.
[4] Abu-Samra A, Morris J S, Koirtyohann S R. Anal. Chem., 1975, 47: 1475 .
[5] Gedye R N, Smith F E, Westaway K et al. Tetrahedron Lett., 1986, 27: 279.
[6] Laurent R, Laporterie A, Dubac J. Organometallics, 1994, 13: 2493.
[7] Aysola P, Ersen P D, Langford C H. Anal. Chem., 1988, 21: 2003.
[8] Akyel C, Bilgen E. Energy, 1989, 14 (12): 839.
[9] Teffal M, Gourdenne A. Eur. Polym. J., 1983, 19: 543.
[10] Dori A D, Huggett R, Bates J F et al. Dent. Mater., 1988, 4: 25.
[11] Stoffer J O, Sitatram S P. Am. Chem. Soc., Proc. Polym. Mater. Sci. Eng., 1994, 71:
55.
[12] Lu J M, Zhu X L, Zhu J et al. J. Appl. Polym. Sci. 1997,
66: 129.
[13] Lu J M, Zhu X L, Zhu J et al. J. Appl. Polym. Sci. 1998, 68: 1563.
[14] Mijovic J, Ijawa J. Polym. Compos., 1990, 11: 184.
[15] Silinski B, Kuzmyca C, Grourdene A. Eur. Polym. J., 1987, 23:273.
[16] Mayo F R, Lewis F M. J. Am. Chem. Soc., 1944, 66: 1594.
[17] Karna S P, Talapatra G B, Wijehun W M K P et al. Phys. Rev. A, 1992, 45: 2763.
[18] Karna S P, Talapatra G B, Prasad P N. J. Chem. Phys., 1991, 95: 5873.
[19] Meyers F, Adant C, Bredas J L. J. Am. Chem. Soc., 1991, 113: 3715.
[20] Meyers F, Bredas J L, Zyss J. J. Am. Chem. Soc., 1992,114: 2914.
|