Characterization and preparation of
nano-sized a-Fe2O3
particles by solid phase method
Du
Yanjun, Du Baoan, Zhao Lei, Lv Jiantong
(College of Chemistry and
Environmental Science, Hebei University, Baoding 071002, China)
Abstract
Nano-sized a-Fe2O3 particles have been attracting great attentions due
to its excellent physical and chemical properties in recent years. In this paper,
nano-sized a-Fe2O3 particles were prepared by solid phase method using
Fe(NO3)3·9H2O and NaOH as
raw materials. A series of experimental researches were carried out in order to obtain the
nano-sized iron oxide powders with mono-phase and good dispersion. X-ray diffraction (XRD) and transmission electron microscopy (TEM) were used to
investigate the products. The best preparation parameters were also obtained through these
series of contrastive experiments. The results from XRD showed that the products were a-Fe2O3.
It could be seen from TEM that their shapes were peanut-like, and the sizes of the
particles were around 50 nm.
Keywords Nano-sized a-Fe2O3;
preparation; characterization; solid phase method
1. INTRODUCTION
Nano-sized a-Fe2O3
particles are widely used as functional materials because of its excellent physical and
chemical properties. There are comprehensive applications in magnetic materials,
gas-sensing materials, catalyst materials and so on [1]. Generally,
nanoparticles of a-Fe2O3 can be prepared by sol-gel method [2,3],
microemulsion method [4], hydrothermal method [1,5], microwave
method [6, 7,8], solid phase method[9], and so on. In the present
paper, nanoparticles of a-Fe2O3 were prepared by solid-phase method
using Fe(NO3)3·9H2O and NaOH as raw materials.
Different experimental conditions were carried out in order to obtain the nano-sized iron
oxide powders with mono-phase and good dispersion. Compared with other methods, the solid phase method
applied for preparation of nano-sized a-Fe2O3 particles has advantages of
low cost of production, simple process and short period of production, which are suitable
for industrial production. We hope that the method described in the paper is useful for
production of nano-sized a-Fe2O3 on industrial scale.
2. EXPERIMENTAL
The nano-sized a-Fe2O3 particles were prepared as
follows: 10 g Fe(NO3)3·9H2O and 3 g NaOH were put
into agate mortar, then were mixed and grinded thoroughly. With grinded, the mixture
became glue gradually, and then solidified. The solidified materials were grinded to
powders, and then washed three times with water and ethanol, respectively. The prepared
materials were decompressing filtered, air dehydration naturally at ambient temperature,
and then the precursors were obtained. Then the precursor was grinded, and calcined for
different period at different temperature. Finally, the products were obtained. The phase
compositions of the products were examined by XRD. The sizes and shapes of the products
were testified by TEM.
3. RESULTS AND DISSCUSSION
3.1 XRD analysis of the nanoparticles of a-Fe2O3
The crystal structure of the five samples were analysed by X-ray diffraction using CuK a radiation (CuKa, lCu = 0.154178 nm). The conditions of calcinations were
showed in Table 1. The XRD patterns of samples were illustrated in Fig. 1.
Table 1. The conditions for
calcinations of the precursors
Samples |
#1 |
#2 |
#3 |
#4 |
#5 |
Temperature and period |
673K 2h |
773K 2h |
873K 2h |
673K 2h , 873K 2h |
573K 2h , 973K 2h |
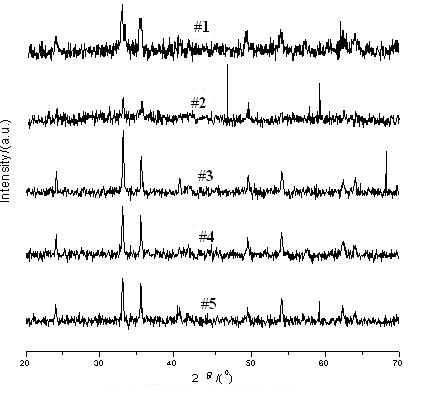
Fig.1 XRD patterns of the samples
According to Fig.1, the sample #1 was α-Fe2O3 and belongs to hexagonally, the shapes
of peaks were in accordance with the other references [1,10]. However, the 3.66
characteristic peak was absent in the XRD pattern of sample #1, which indicated some
impurity of g -Fe2O3 was contained in sample #1. Thus, pure a-Fe2O3
nano-sized particles could not be obtained by calcining the precursor for 2h at 673K. On
the other hand, the reaction reagents could not be changed into a-Fe2O3
completely due to the lower temperature and shorter period, some impurities and the
residual precursor still remained in sample #1 [6]. The sample #2 was better
than the sample #1, although some impurities were still contained in the sample #2.
According to Fig.1, the sample #3, #4 and #5 were pure a-Fe2O3.
Seen from Fig. 1, with the temperature of calcinations ascending and
the period extending, the X-ray diffraction peaks became higher and narrower. The average
sizes of particles were calculated by the Scherrer formula:
D = k·l/(b·COS q)
where D (nm) is the primary diameter of the product, k equals 1.075, lCu (nm) is
0.154178, b(arc) is integral peak width, q (degree) is angle of diffraction. X-ray diffraction peaks with low
angular degree (generally 2q ≤50°) were selected for calculation, and the average value was
obtained. These results were showed in Table 2. From Table 2, it could be seen that the
primary diameter of particles was in the range of 20-30 nm.
Table 2. Average primary
diameter of samples by calculation according to XRD data
Samples |
#1 |
#2 |
#3 |
#4 |
#5 |
D (nm) |
20.004 |
25.786 |
23.339 |
26.922 |
25.110 |
3.2 TEM analysis of nano-sized
particles of a-Fe2O3
The TEM photograph of sample #3 was shown in Fig. 2. According to Fig. 2, the sizes of the
particles were about 50 nm and their shapes were peanut-like. The TEM photographs of the
other samples were similar to Fig. 2, so these photographs were not shown in the present
paper. Commonly, the calculated primary diameter based on XRD was less than the primary
diameter based on TEM, our result was accordant with this phenomenon in this study.
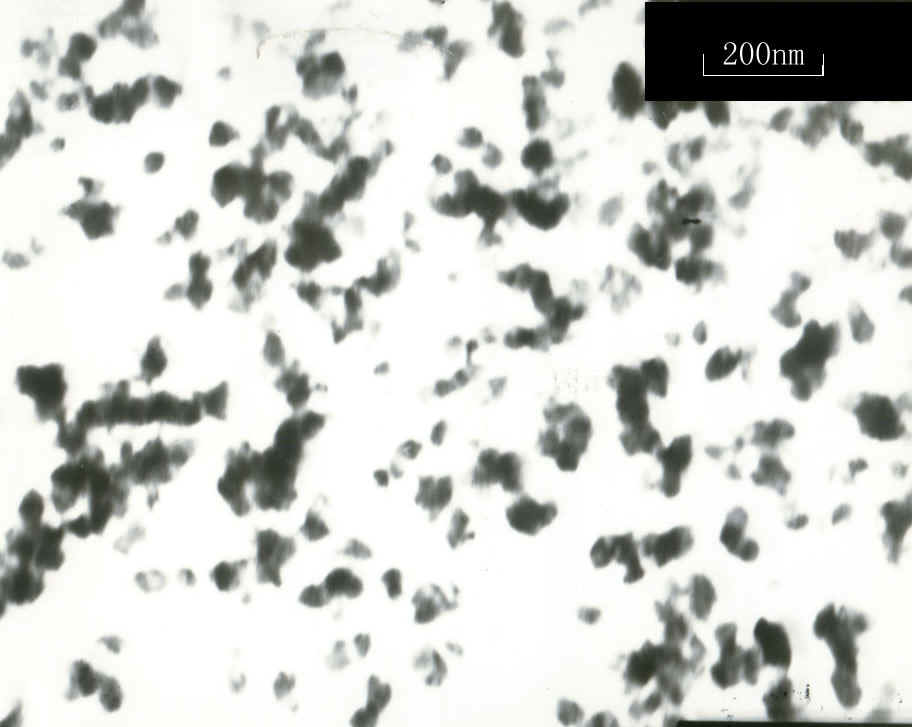
Fig. 2 The TEM photograph of
sample #3
3.3 Optimization of temperature and
period of calcinations
The temperature and period of calcinations were important factors for preparation of
nano-sized a-Fe2O3 particles. Pure and uniform Fe(OH)3 began
to decompose at 575.1K, a-Fe2O3 emerged at 573-673K, with the
temperature ascending constantly, Fe(OH)3 decomposed completely at 873K 2h,
then a-Fe2O3
was obtained. With the temperature ascending and the period extending, the sizes of a-Fe2O3
particles become larger. Finally, the temperature of 873K and the period of 2h were chosen
for preparation of nano-sized a-Fe2O3 particles.
3.4 Mechanism of preparation of nano-sized particles by solid-phase method
The mechanism can be described by the following two steps:
Fe(NO3)3·9H2O + 3 NaOH Fe(OH)3 + 3NaNO3 +9H2O
2Fe(OH)3 a-Fe2O3 +3H2O
In the process of solid-phase reaction, the contact area of reagents
becomes larger by grind; meanwhile the temperature of some area ascends, which can
initiate reaction of the reagents. Crystal water was included by Fe(NO3)3·9H2O
and the melting point of Fe(NO3)3·9H2O was low,
therefore the trace crystal water can be used as space of accelerating the reaction. The
particles collided with each other and nucleuses were formed rapidly, but particles were
very difficult to cross every phase, therefore the nucleuses could not grow rapidly.
According to the theories of crystal science, when the speed of forming nucleuses far
exceeded the speed of growing of nucleuses, small particles can be formed easily.
Therefore solid-phase method was a good way for preparation of nano-sized particles.
4. CONCLUSIONS
In this study, nano-sized a-Fe2O3 particles were prepared by
solid phase method using Fe(NO3)3·9H2O and NaOH as
raw materials. The prepared production was characterized by X-ray diffraction and
transmission electron microscopy. The experiment showed that the temperature and period of
calcinations were important factors influencing preparation of nano-sized a-Fe2O3
particles. The best preparation parameters were also obtained through contrastive
experiments. The results from XRD showed that the products were a-Fe2O3.
It could be seen from TEM that their shapes were peanut-like, and the sizes of the
particles were around 50 nm. The technology for preparation of nano-sized a-Fe2O3
particles by solid phase method had advantages of low cost of production, simple process
and short period of production, which were suitable for industrial production.
REFERENCES
[1] Wu D.H., Zhang Z.X., Xu L.F., et al. Chinese Journal of Inorganic
Chemistry, 2004, 20(1): 31-36.
[2] Wang Y.S., Li J.. Journal of Inorganic Materials, 1998, 13(5): 745-750.
[3] Sugimoto
T., Muramatsu
A., Muramatsu
A.. Journal
of Colloid and Interface Science, 1993, 159:
372-382.
[4] Chen L.W., Gan L.H., Yue T.Y., et al. Acta Physico-Chimica Sinica, 1994, 10(8):
750-754.
[5] Wang X.Y., Kang X.H., Xie H.Q., et al. Chinese Journal of Applied Chemistry, 2004,
21(7): 655-659.
[6] Jia Z.B., Wei Y., Wang H.M.. Journal of Inorganic Materials, 2000, 15(5): 926-928.
[7] Fu Z., Hao X.S., Wu Z.C., et al. Chinese Journal of Inorganic Chemistry, 1999, 12(2):
219-222.
[8] Dong D.C.,
Dai S.S., Dai S.S. Materials
Research Bulletin, 1995, 30(5): 531-535.
[9] Qiu C.X., Jiang J.S., Zhao Z.J., et al. Journal of Inorganic Materials, 2001, 16(5):
957-960.
[10] Wei Y., Liu X.L., Zheng X.Z.. Acta Physico-Chimica Sinica, 1996, 12(6): 551-553.
纳米α-Fe2O3粒子的固相法制备和表征
杜艳君,杜宝安,赵磊,吕建通
(河北大学化学与环境科学学院,保定,071002)
摘要 由于纳米a-Fe2O3粒子具有良好的物理化学性质,因此一直受到相关领域科学家的广泛关注。在本文中,以Fe(NO3)3·9H2O和NaOH固体为原料,采用固相法制备了a-Fe2O3纳米粒子。为了制备单相、分散性好的产品,进行了一系列的实验条件摸索。利用X射线衍射(XRD)和透射电子显微镜(TEM)对产品进行了表征。通过实验比较,优化了制备条件。经XRD检测,表明产品为a-Fe2O3,TEM显示a-Fe2O3粒子外形呈花生状,粒径约为50 nm。
关键词 纳米a-Fe2O3;制备;表征;固相法
|