Synthesis and
characterization of poly (butylene terephthalate)-poly(ethylene terephthalate- co-
isophthalate- co- sebacate) segmented copolyesters
Zhao Yunhui, Sheng
Jing
(School of Materials Science and Technology, Tianjin University, Tianjin 300072, China)
Abstract This paper described the
preparation of quarternary segmented copolyesters involving bulk polyester produced on
large scale-poly(butylene terephthalate) (PBT) and ternary amorphous random copolyester
poly(ethylene terephthalate-co-isophthalate-co-sebacate) (PETIS) by means of melting
transesterification processing under vacuum condition. Investigations on thermal
properties, crystal structures, and crystallization morphology were undertaken by
differential scanning calorimetry (DSC), wide angle X-ray diffraction (WAXD), and
polarized light microscope (PLM), respectively. Nuclear magnetic resonance (NMR) was used
in the analysis of copolyesters compositions.The results showed that melting
transesterification was an available method to synthesize segmented copolyesters for
potential application. The final composition in quarternary copolyesters was approximately
equal to the feed ratio. The location of melting and crystallization peaks depended on
both feed ratio and reaction time. Reasonable sequence length of copolyester segments,
which should give rise to higher melting and crystallization temperatures, might be
present in samples with shorter reaction time and higher ternary copolyester content. The
optical micrograph exhibited three-dimensional spherulitic growth.
Keywords segmented copolyester, melting transesterification, poly (butylene
terephthalate) (PBT), poly (ethylene terephthalate- co- isophthalate- co-sebacate) (PETIS)
1 INTRODUCTION
Copolyesters, because of their low price and versatile properties for application, have
drawn much attention for many years. Most of them are binary or ternary random copolymers,
and have been studied extensively by researchers[1-3]. In practice, synthesis
of segmented copolyesters with crystallizing segments is an effective way to obtain new
polyester material, because regulation of the crystal structure offers an addition
possibility of optimizing their properties[4]. Two methods have often been
employed to synthesize segmented copolyesters[5]. One is the coupling of
prepolymers with relatively low molecular weight, the other is the transesterification by
melting processing between bulk homopolymers.
The addition of aliphatic polyesters in copolyester might render it
potential application in elastic fiber and thermoplastic resin with strike properties.
Aliphatic polyesters can be used alone or in combination with other polyesters as soft
segment to provide elasticity. Recently, in our laboratory we have synthesized a series of
segmented copolyesters involving one of the most available polyesters-poly (butylene
terephthalate) (PBT) and ternary amorphous random copolyester-poly (ethylene
terephthalate-co-isophthalate-co-sebacate) (PETIS) by means of melting
transesterification. The fractions of PETIS random copolymer ranged from 60-80% wt % (with
the contents of aliphatic polyester PES ranging from 24-28% wt %). This suggests the
formation of copolyesters with moderate elasticity.
Since reaction time plays an important role in melting
transesterification, polymerization experiments were carried out at different time for
each composition. Investigations on melting and crystallization behaviors were undertaken
by differential scanning calorimetry (DSC). To confirm the difference in copolyester
composition, we performed the 1H-nuclear magnetic resonance (NMR) measurements.
Wide angle X-ray diffraction (WAXD) was used in the analysis of crystalline structure.
2 EXPERIMENTAL
2.1 Materials
PBT chips were kindly supplied by Yi Zheng Chemical Fiber Co., China. Dimethyl
terephthalate (DMT), ethyl glycol (EG), isophthalate acid (IPA), sebacate acid (SA), zinc
acetate (Zn(OAC)2),
and tetrabutyl orthotitanate (TBT) were all reagent grade and used as received.
2.2 Synthesis of PETIS random copolyesters and
PBT-PETIS segmented copolyesters
The synthesis of ternary amorphous random copolyesters can be divided into two steps. The
first involves the transesterification of DMT and EG with zinc acetate as a catalyst, and
the esterification of SA, IPA and EG, yielding bis(hydroxyethyl) terephthalate (BHET),
bis(hydroxyethyl) sebacate (BHES), and bis(hydroxyethyl) isophthalate (BHEI). The second
one is the principal reaction leading to the formation of copolyester by means of
polycondensation in the presence of tetrabutyl orthotitanate (TBT) as a catalyst.
The melting transesterification between PBT and PETIS was conducted in
a four-neck flask equipped with a mechanically sealed stirrer and condenser under nitrogen
atmosphere and vacuum condition less than 133Pa. The melting processing was proceeded
isothermally at 255°C for 10min, 20min, 40min, and 60 min, respectively. The
process is given in Scheme1.

PETIS
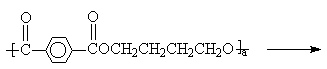
PBT

PBT-PETIS
Scheme 1
2.3 Characterization of PBT-PETIS segmented
copolyesters
The intrinsic viscosity was determined at 25±0.1°C in a phenol/1,1,2,2-tetrachloroethane (50/50, w/w) solution with a
concentration of 0.5g/100ml by an Ubbelohde viscometer, and the density was measured with
a gradient density column in a thermostat at 25±0.1℃ using
aqueous solution of sodium bromide. Different Scanning Calorimetry (DSC) measurement was
carried out on a Shimadzu-50 apparatus calibrated with Al2O3 under
nitrogen atmosphere using samples of about 5mg. The sample was heated up to 30°C above the melting temperature at a rate of 10°C/min, and maintained for 5 min to erase the thermal
history, and then cooled down at a rate of 10°C/min to room temperature. Wide angle X-ray
diffraction measurement (WAXD) was done on melt-pressed films in the reflection mode with
a Rigaku diffractmeter using Ni-filtered Cu-Ka radiation. The 1H-nuclear
magnetic resonance spectra (NMR) were recorded with a Varian UNITY-plus400MHz NMR
spectrometer by dissolving samples in deuterated chloroform (CDCl3).
Copolyester sample was sandwiched in between two pieces of glass slides followed by
melting completely. Then the specimen was rapidly quenched to the predetermined
crystallization temperature and maintained for 2 hours. Crystalline morphology of
copolyester was investigated using a polarized light microscopy (PLM).
3 RESULTS AND DISCUSSION
Segmented copolyesters at room temperature
appear soft or hard semi-crystalline solids according to compositions. The samples with
varying compositions are given in Table 1, where intrinsic viscosity and density are also
reported.
The values of intrinsic viscosity demonstrate that melting
transesterification is available and yields copolyesters having molecular weights high
enough for usual application. Moreover, because of the high values of intrinsic viscosity,
effect caused by the discrepancy of molecular weight on properties can be negligible. The
density had a little variation for samples with different reaction time, but increased
slightly with increasing PBT content in segmented copolyesters.
All copolyester samples show lower melting peaks compared to the PBT homopolymer.
The depression of melting temperature is due to the limited crystallite size and to the
larger amount of crystal imperfection because of the less favourable crystallization
conditions[6]. DSC curves in the heating run reveal double melting peaks for
PBT-rich copolyesters, which is however a widespread observation that has been reported in
the literatures[7,8]. Park and Kang[9] pointed out that the lower
one can be attributed to melting of PBT crystal related to ternary random copolyester, and
the other to that of pure PBT crystal. Rim and Runt[10], however, thought that
the multiple-melting endotherms may result from reorganization processes. They explained
the phenomenon as follows: the low-temperature endotherm reflects the true melting
behavior of the as formed crystals while the higher temperature endotherm represents the
melting of material that has undergone annealing upon heating. For comparison, endothermic
peaks were presented in Fig.1 according to reaction time. Table II collected the summary
of corresponding thermal properties. The double melting peaks are marked Tm1
and Tm2 in Table II respectively, and DHm
is the heat of fusion; Tc and DHc are the maximum
and the enthalpy of exothermic peak, respectively.
Table 1 Designated Samples and Their
Intrinsic Viscosity and Density
Samples |
Feed ratio (wt %)
(PET/PEI/PES) = 40/20/40 |
Reaction time (min) |
Intrinsic viscosity
(dL·g -1) |
Density
(g ·cm -3) |
PBT |
PBT/(PET/PEI/PES) |
PBT |
100 |
100/(0/0/0) |
|
0.8000 |
1.2795 |
20PBT-10 |
20 |
20/(32/16/32) |
10 |
0.5930 |
1.2596 |
20PBT-20 |
20 |
20/(32/16/32) |
20 |
0.5860 |
1.2591 |
20PBT-40 |
20 |
20/(32/16/32) |
40 |
0.6231 |
1.2596 |
20PBT-60 |
20 |
20/(32/16/32) |
60 |
0.6350 |
1.2601 |
30PBT-10 |
30 |
30/(28/14/28) |
10 |
0.5213 |
1.2642 |
30PBT-20 |
30 |
30/(28/14/28) |
20 |
0.5647 |
1.2637 |
30PBT-40 |
30 |
30/(28/14/28) |
40 |
0.6074 |
1.2634 |
30PBT-60 |
30 |
30/(28/14/28) |
60 |
0.5617 |
1.2640 |
40PBT-10 |
40 |
40/(24/12/24) |
10 |
0.6030 |
1.2679 |
40PBT-20 |
40 |
40/(24/12/24) |
20 |
0.5955 |
1.2687 |
40PBT-40 |
40 |
40/(24/12/24) |
40 |
0.6536 |
1.2671 |
40PBT-60 |
40 |
40/(24/12/24) |
60 |
0.6502 |
1.2689 |
PETIS |
0 |
0/(40/20/40) |
150 |
0.4866 |
1.2476 |
From
Table 2, we can find that all DSC curves show melting peak whose location depends on both
the composition and reaction time. Firstly, melting peaks gradually move to lower
temperature region and become wider when the content of PBT segment is increased. High
feed fraction of amorphous copolyester PETIS should give rise to relatively long sequence
of soft segment, which might favor forming of regular crystals of PBT. On the other hand,
relatively short amorphous random copolyester segments, which during melting
transesterification are generated from low feed fraction of amorphous copolyester, might
act as crystal imperfection. As a result, the melting temperatures are depressed, and this
is the reason for wider range of melting peaks. Secondly, for a chosen composition, sample
with shorter reaction time revealed higher melting temperature than those of with longer
reaction time. Extended reaction time promoted shorter sequence length of polyesters[10],
which result in lower melting temperatures. Moreover, the broadened distribution of
sequence length caused by prolonged reaction time is the reason for wide range of melting
temperature.
In the same manner, lower crystallization temperatures are presented in
PBT-rich samples as well as samples with longer reaction time. The depression of Tc
is seemingly because of the incorporation of short sequence length of noncrystallizable
copolyester segments generated by decreased amorphous polyester content and prolonged
reaction time.
Table 2 Characteristic Data of Melting
and Crystallization
Samples |
Tm1
( °C) |
Tm2
( °C) |
Tm,onset
( °C) |
Tm,endset(°C) |
DHm
(J·g -1) |
Tc
( °C) |
Tc,onset
( °C) |
Tc,endset
( °C) |
DHc
(J·g -1) |
PBT |
-a |
225.29 |
206.57 |
238.28 |
43.76 |
183.43 |
194.84 |
173.21 |
42.51 |
20PBT-10 |
- |
224.70 |
204.81 |
231.87 |
14.47 |
177.56 |
185.77 |
171.39 |
11.07 |
20PBT-20 |
- |
220.88 |
200.13 |
229.19 |
13.30 |
170.61 |
179.13 |
163.99 |
10.46 |
20PBT-40 |
- |
214.40 |
147.55 |
225.15 |
13.66 |
160.29 |
169.63 |
153.28 |
10.83 |
20PBT-60 |
- |
182.20 |
140.87 |
209.48 |
6.44 |
126.97 |
139.99 |
117.03 |
5.95 |
30PBT-10 |
197.20 |
214.46 |
187.21 |
225.21 |
18.31 |
164.73 |
173.44 |
155.75 |
13.86 |
30PBT-20 |
186.72 |
200.09 |
157.89 |
214.89 |
16.10 |
145.70 |
155.68 |
137.31 |
13.31 |
30PBT-40 |
176.58 |
187.52 |
135.32 |
206.50 |
16.60 |
131.92 |
143.63 |
123.24 |
12.77 |
30PBT-60 |
171.81 |
176.09 |
124.84 |
200.54 |
15.02 |
129.29 |
140.29 |
120.35 |
10.10 |
40PBT-10 |
200.07 |
212.36 |
180.95 |
222.89 |
20.06 |
159.43 |
169.45 |
149.52 |
17.82 |
40PBT-20 |
184.98 |
198.87 |
157.14 |
213.85 |
22.91 |
142.92 |
152.95 |
134.04 |
17.67 |
40PBT-40 |
168.09 |
173.86 |
135.19 |
207.34 |
18.30 |
124.05 |
137.81 |
114.31 |
15.91 |
40PBT-60 |
168.50 |
184.46 |
131.71 |
194.78 |
15.13 |
116.19 |
129.64 |
106.65 |
15.44 |
a : not
detected
In the
WAXD patterns of PBT, five diffraction peaks, namely, 16.1 o, 17.2 o,
20.6 o, 23.1 o, and 25.2 o are assigned for the ( ), (010), ( ), (100), and ( ) plane, respectively. With the increasing content of
amorphous copolyester PETIS, the diffraction peaks tend to be broaden, but still exihibit
the PBT-related scattering angles. The patterns for samples with 30% PBT(wt%) at various
reaction time shown in Fig.2 confirm that reaction time has intensive influence on melting
transesterification processing. The intensity of diffraction peaks become weaker as the
reaction time is prolonged, which infers the change from segmented into random by the
interchange between two different kinds of polyesters. Attempt has been made to divide
patterns into separate Gaussian profiles, and then crystallite dimensions can also be
calculated by using Scherrer equation as follows:[12]
(1)
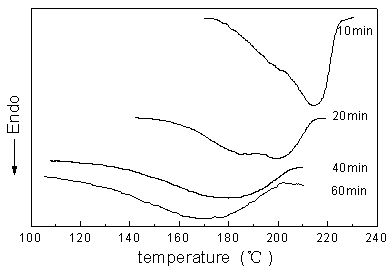
Fig.1 melting endotherms of sample
with 30% PBT (wt %) (reaction time indicated) |
|
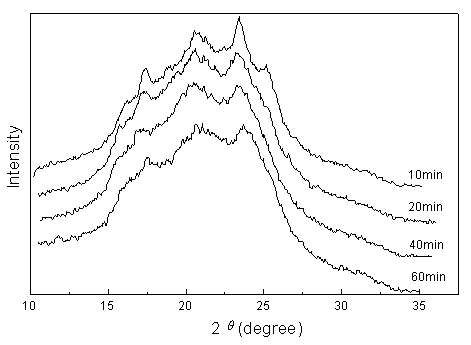
Fig.2 WAXD patterns of sample with 30% PBT (wt %) (reaction time indicated) |
|
where D is the mean crystallite dimension; q , the Bragg angle; l , the
wave length (0.1542nm); b , the half-high breadth at the Bragg scattering angle;
and k is a constant (0.89). The calculation was done only for the (010), ( ), and (100) planes whose Bragg angle is quite clear in
the patterns. Table 3 collected the crystallography data. The dimensions of segmented
copolyesters are very smaller than those of PBT homopolymer for which the melting behavior
provided early indication, but there is a trace discrepancy among segmented copolyester
samples.
Table 3 Crystallography Data of WAXD
Samples |
(010) |
( ) |
(100) |
2q(o) |
b(o) |
D(nm) |
2q(o) |
b(o) |
D(nm) |
2q(o) |
b(o) |
D(nm) |
PBT |
17.2 |
2.211 |
3.597 |
20.6 |
1.859 |
4.299 |
23.1 |
1.662 |
4.829 |
20PBT-10 |
17.1 |
2.938 |
2.707 |
20.2 |
2.582 |
3.094 |
23.7 |
4.917 |
1.634 |
20PBT-20 |
17.8 |
3.450 |
2.307 |
20.6 |
2.293 |
3.485 |
23.6 |
4.342 |
1.850 |
20PBT-40 |
17.5 |
3.252 |
2.447 |
20.4 |
2.397 |
3.334 |
23.3 |
3.717 |
2.160 |
20PBT-60 |
17.2 |
3.301 |
2.409 |
20.5 |
3.018 |
2.648 |
23.7 |
2.830 |
2.839 |
30PBT-10 |
17.5 |
2.953 |
2.694 |
20.9 |
2.918 |
2.740 |
23.5 |
2.916 |
2.720 |
30PBT-20 |
17.5 |
3.291 |
2.418 |
20.4 |
2.105 |
3.796 |
23.5 |
3.571 |
2.249 |
30PBT-40 |
17.4 |
3.618 |
2.199 |
20.4 |
2.407 |
3.320
|
23.5 |
3.205 |
2.506 |
30PBT-60 |
17.7 |
3.888 |
2.047 |
20.7 |
2.398 |
3.335 |
23.8 |
3.661 |
2.195 |
40PBT-10 |
17.3 |
2.977 |
2.672 |
20.2 |
2.047 |
3.903 |
23.4 |
3.453 |
2.326 |
40PBT-20 |
16.8 |
3.004 |
2.646 |
20.4 |
1.920 |
4.161 |
23.6 |
2.895 |
2.775 |
40PBT-40 |
17.7 |
2.970 |
2.680 |
20.4 |
2.316 |
3.450 |
23.6 |
3.317 |
2.422 |
40PBT-60 |
17.5 |
3.798 |
2.095 |
20.4 |
2.428 |
3.291 |
23.5 |
3.236 |
2.482 |
Although sequence
distribution in the copolyester chain is very important to the understanding of its
chemical structure, only a few papers[9,13] reported the investigation on
sequence distribution between aromatic polyester and ternary or binary aliphatic
copolyesters. One technical problem associated with is the interchange between PBT and
PETIS may result in very complex constitution. Investigation on sequence distribution is
being conducted. The analysis of NMR in this work is in progress for testing the
composition on PBT-PETIS. Fig.3 shows the spectra of PBT homopolymer, PETIS random
copolyester, and segmented copolyester 30PBT-40. Assignments of proton signals are listed
in table 4.
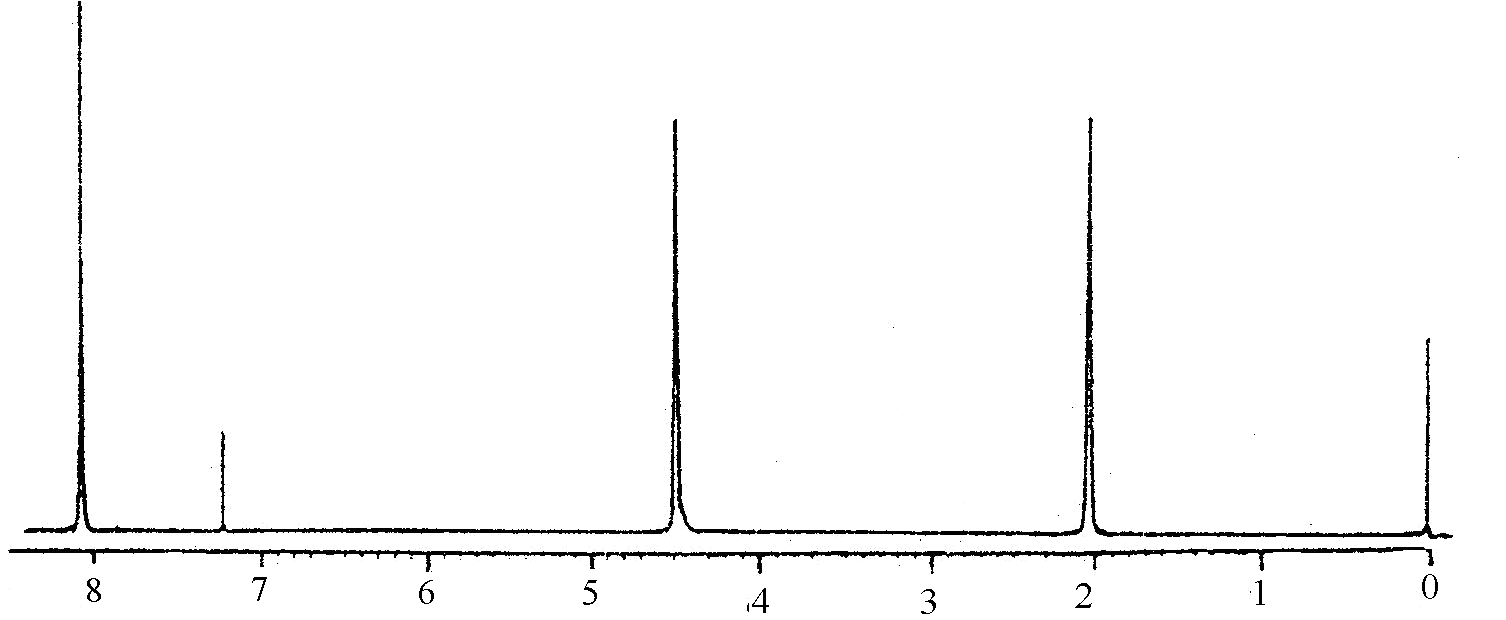
PBT
PETIS
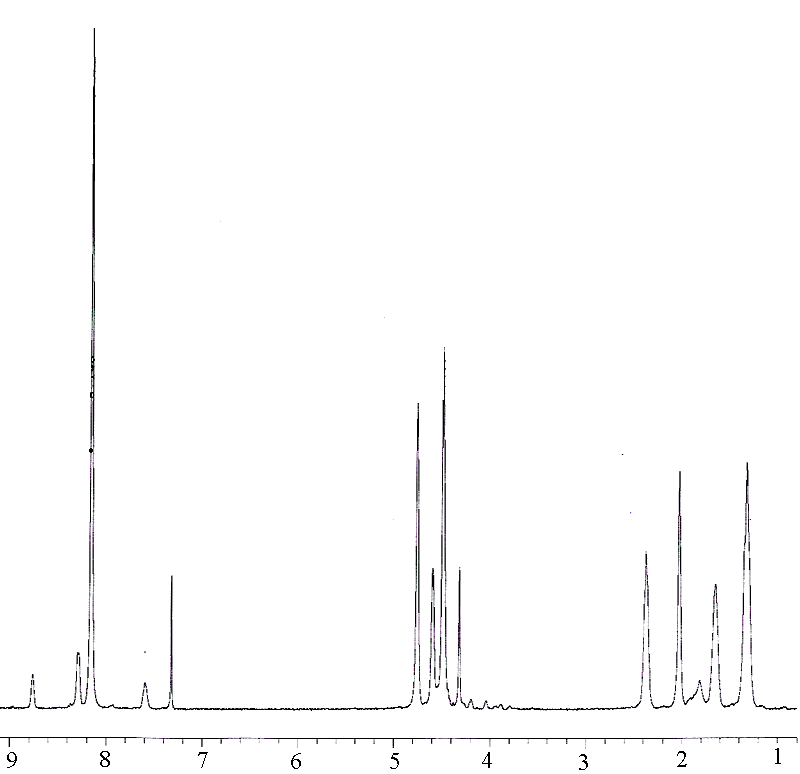
30PBT-40
Fig.3 1H-NMR spectra
Table 3 Assignments of Proton Signal and
Their Chemical Shift in the 1H-NMR Spectra
|
PBT |
PETIS |
PBT-PETIS |
d (ppm) |
δ (ppm) |
e |
δ (ppm) |
e |
I1 |
|
8.758 |
3.14 |
8.761 |
3.00 |
I2 |
|
8.293 |
7.20 |
7.295 |
6.95 |
I3 |
|
7.597 |
3.16 |
7.595 |
3.41 |
T b |
8.09 |
8.160 |
24.66 |
8.148 |
46.13 |
A1 |
|
2.371 |
22.76 |
2.373 |
21.81 |
A2 |
|
1.644 |
23.22 |
1.649 |
21.73 |
A3 |
|
1.320 |
46.94 |
1.322 |
43.85 |
X1 |
4.43 |
|
|
4.486 |
21.23 |
X2 |
1.97 |
|
|
2.028 |
21.44 |
X3-X5 |
|
4.751 |
23.96 |
4.753 |
25.09 |
|
|
4.478 |
14.10 |
4.486 |
14.10 |
|
|
4.589 |
16.52 |
4.592 |
15.17 |
|
|
4.314 |
8.69 |
4.316 |
7.30 |
b:
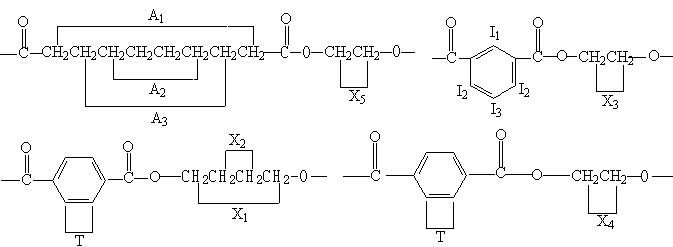
The peaks at 1.32-2.37 ppm were assigned to the protons in sebacate
group, and the ethylene proton resonance of PES units which are located at 4.31-4.75 ppm
overlapped with the ethylene proton peak of PEI units in PETIS. When the PBT units were
introduced, the chemical shift attributed to protons in the tetramethylene unit appear at
2.03 and 4.49 ppm, and also the final composition was confirmed by NMR data. The molar
ratio of PBT: PET was about 1.1486:1, which approximates the feed ratio 1.0694:1.

20PBT-20
30PBT-20
40PBT-20
Fig.4 optical micrographs of
samples
Spherulite morphology of PBT homopolymer has been observed by Stein[14] to have
two types. One leads to growth of unusual spherulite at low temperature, and the other to
usual spherulite at high temperature. In copolyesters, the two types of spherulites may be
somewhat more indistinct, coexist together, and a transitional spherulite is favoured.
Early work by Keith and
Padden[15] proposed a parameter to characterize the internal morphology of a
spherulite:
(2)
where B is the
diffusion coefficient for noncrystallizable content; and G, the radial growth rate
of the spherulite. For high concentration of noncrystallizable polyester PETIS, since the
PETIS repeating units enter the PBT main chain to a minor degree on the process of melting
transesterification for causing the long sequence length of PETIS segments and the high
growth rate of crystals, may it be supposed that, in the formation of the crystals, the
spherulites not only pack themselves densely, but also form finer fibrils. Consequently,
the value of s decreases and optical micrograph of PBT-PETIS samples reported in Fig.4
showed nice spherulite images in copolyesters with 20%PBT and 30%PBT. Conversely, the
spherulitic character is not evident for samples with relatively lower concentration of
noncrystallizable polyester.
Acknowledgement The
authors acknowledge the financial support of Petrochemical Co., China.
REFERENCES
[1] Yu J Y, Li B Z, Lee S W. J Appl Polym Sci, 1999, 73: 1191.
[2] Lotti N, Finelli L, Fiorini M. Polymer, 2000, 41: 5297.
[3] Tsai H B, Chang S J, Chen M S. Polymer, 1990, 31: 1589.
[4] Godovsky Y, Yanul N A, Bessonsva N P. Colloid Polym Sci, 1991, 269: 901.
[5] Cheng X M, Luo X L, Li Z B, et al. J Polym Sci, Polym Chem, 1999, 37: 3770.
[6] Gabriëlse W, Soliman M, Dijkstra K. Macromolecules, 2001, 34:
1685.
[7] Park S S, Chae S H, Im, S S. J Polym Sci, Polym Chem,
1998, 36: 147.
[8] Marrs W, Peters R H, Still R H. J Appl Polym Sci, 1979, 23: 1063.
[9] Park S S, Kang H J. Polym J, 1999, 31: 238.
[10] Rim P B, Runt J P. Macromolecules, 1983, 16 (5): 762.
[11] Yamadera R, Murano M. J Polym Sci, Part A-1, 1967, 5: 2259.
[12] Alexander L E. X-ray Diffraction Method in Polymer Science, Krieger R E Publ. 1979.
[13] Kang H J, Park S S. J Appl Polym Sci, 1999, 72 (4): 593.
[14] Stein R S, Misra A. J Polym Sci, Polym Phys Ed, 1980, 18: 327.
[15] Keith H D, Padden F J Jr. J Appl Phys, 1963, 34: 2409.
|